Как сделать корпус усилителя
Поперто отсюда. Часть про схемотехнику нещадно вырезана — это мы и сами умеем.
Сделать усилитель не так сложно, как это кажется. Все работы можно выполнить дома на кухне, располагая минимальным набором инструмента и материала. Но тем не мене можно получить впечатляющие результаты. В этой статье я расскажу вам, как это сделать. Я так же не буду пользоваться станками и выполню все работы вручную.
Для корпуса понадобится алюминиевый угольник 15Х15 миллиметров, можно и больше, но не меньше, а то корпус не будет обладать достаточной жёсткостью. Сначала надо нарезать заготовок.
Рекомендую сначала нарисовать корпус на бумаге и просчитать все размеры, что бы потом не было мучительно больно. Когда я делаю корпуса, то исхожу из того, что все стандартные аппараты Hi-Fi класса имеют корпуса длиной 430 или 460 миллиметров, при этом их высота и глубина не лимитируется. Размер 460 миллиметров мне кажется великоватым, по этому, я принял размер 430 миллиметров. Сам корпус планирую отделать стеклом толщиной 4 миллиметра. Из этого следует, что каркас должен быть меньше по размерам, чем окончательный размер усилителя. Если будет крышка из стекла 4 миллиметра и днище из алюминия толщиной 1.5 миллиметра, то высота каркаса должна быть на 5.5 миллиметра меньше планируемого размера. А если сделать стеклянными боковины, то из общей длины надо вычесть две толщины стекла.
Ну вот, заготовки нарезаны, можно приступать к обработке. Начнём с вертикальных стоек каркаса. Тут тоже надо не забыть о том, что от их высоты надо вычесть две толщины полочки применяемого угольника. В моём случае, при общей толщине усилителя 60 миллиметров, толщине стеклянной крышки 4 мм, днища 1.5 мм и толщине полочки угольника получилась высота стойки 51.5 миллиметров.
Все стойки я обрабатывал пакетом, это позволит получить их одинаковую высоту.
Когда стойки будут готовы, приступаем к обработке горизонтальных элементов каркаса. Каждый конец угольника надо спилить под углом 45 градусов для удобной состыковки. Отчертить можно по школьному угольнику (я же обещал не пользоваться профессиональным инструментом).
Обратите внимание на две следующие фотографии, на них видно, как надо спиливать конец угольника.
Скос должен переходить на полочку, образуя острый угол. Можно предварительно отпилить большую часть металла ножовкой, а окончательно довести напильником. Следите за тем, чтобы все похожие детали были одной длины. Для сборки корпуса размерами 430Х250Х60 понадобится четыре угольника длиной 422 миллиметра, и четыре угольника длиной 250 миллиметров. Через час у меня были все заготовки сделаны, и я приступаю к сборке каркаса.
Собирать буду на винтах М3, можно было и склепать, но заклёпки сейчас стали дефицитом, а тяговые для этого дела не подходят – у них будет торчать головка. Винты надо купить с потайной головкой и заточить сверло под угол 90 градусов для высверливания углублений под головку винта.
Два угольника собираются на одной вертикальной стойке, так, как показано на снимке.
А это вид с обратной стороны.
Для большей точности, можно сверлить зажав детали в тиски.
Должно получиться нечто, похожее на аквариум.
Теперь надо изготовить днище и заднюю стенку. Я их делал из алюминиевого листа толщиной 1.5 миллиметра. Но можно применить кровельное железо или оргстекло — хуже не будет. Только придётся пересчитать высоту стоек. Для выпиливания заготовок я применил электролобзик, но можно их вырезать любым доступным способом.
При вырезке не старайтесь сразу попасть в размер, лучше сделать на миллиметр больше и окончательно подогнать по месту выступающий край. Вот, днище готово. Его надо прикрутить к каркасу винтами с шагом не более ста миллиметров, это исключит его прогиб.
Вот теперь можно спилить в размер выступающую часть днища.
Так же делается задняя часть корпуса. На ней будут установлены разъём питания, входные и выходные гнёзда. Их надо приобрести заблаговременно.
Размечаем и сверлим отверстия в задней стенке.
Ну, тут всё просто – отверстия круглые, а вот с разъёмом питания придётся повозиться.
Размечаем место под будущее окно и тонким сверлом сверлим отверстия как можно ближе друг к другу. Потом бокорезами перекусываем перемычки…
Пять минут работы напильником и окно готово!
Теперь подумает о ножках нашего будущего усилителя. Их можно применить готовые от старого компьютерного корпуса, но я нашёл ножки от чемодана, которые сделаны из мягкого пластика. Они подошли как нельзя лучше.
Можно приступить к изготовлению передней панели. Я её сделал из алюминиевой полосы толщиной 5 миллиметров, но это не критично, можно и тоньше, просто толстая панель смотрится как-то красивее.
На снимке можно рассмотреть некую разметку, это то, о чём я забыл сказать. Конкретно в этом усилителе, я захотел сделать стрелочный индикатор уровня. Должна же быть какая-то изюминка. Но можно обойтись и без индикаторов, кто не будет их делать – может смело пропустить всё описание про индикаторы.
И разобрал их…
Из них нам понадобится только сам механизм. Вот с ним надо обращаться с максимальной аккуратностью.
Для придания индикатору профессионального вида мы их объединим в одном корпусе и сделаем подсветку. На алюминиевую пластину переносим разметку с оригинального шильдика и выпиливаем надфилем.
И ещё надо изготовить планку, которая прикроет механизм от посторонних взглядов.
Должно получиться что-то типа того, что видно на фотографии.
Стоит обратить внимание на боковые крышки – они нужны для завершения конструкции. И ещё три отверстия в центре – там будут располагаться светодиоды индикации включённого входа. Вот так это выглядит с обратной стороны.
Вся конструкция держится на угольнике, который находится посередине. Подсветка буде осуществляться полоской из синих светодиодов. Они располагаются в верхней части корпуса, над индикатором.
В отверстия, расположенные в центре индикатора, надо вклеить три светодиода красного цвета свечения.
После отвердения клея, рекомендую покрыть его чёрной краской, это позволит избежать паразитной засветки от соседних светодиодов.
Ну и на выводы припаиваем плату с резисторами. Сами светодиоды подключаются параллельно обмоткам реле на плате коммутации.
Под индикатор надо прорезать окно, воспользуемся той же технологией, что и прорезании окна под разъём питания. Только тут надо проявить максимум аккуратности и терпения – от этого будет зависеть внешний вид усилителя.
Тут я не удержался и профрезеровал с обратной стороны углубление под стекло, но это не является обязательным. Можно применить тонкую прозрачную плёнку для лазерных принтеров, эта плёнка очень тонкая и не повлияет на размеры, что не сказать о стекле.
Отверстия под кнопки просверлены сверлом 8.4 миллиметра. Это потому, что у меня есть алюминиевый пруток диаметром восемь миллиметров, из него получатся отличные кнопки.
Фаску в отверстии лучше всего сделать при помощи зенкера, сверлом трудно добиться ровной поверхности.
Сама кнопка отпиливается от прутка нужной длины и шлифуется вручную при помощи ручной дрели. С обратной стороны надо просверлить отверстие 4 миллиметра. Торец желательно отполировать.
Выключатель питания крепится на двух длинных винтах, это позволит точно выставить его высоту для того, чтобы кнопка не тёрла в отверстии.
Но мне она не нравится, я применил самодельную. У кого есть знакомый токарь – советую обратиться к нему за помощью и сделать вот такую ручку.
И для полной завершённости надо изготовить декоративное кольцо.
В сочетании с ручкой это примет вполне законченный вид.
Но ещё раз скажу – это не обязательно, отлично будет смотреться и с другой ручкой. Осталась работа над отделкой корпуса. Переднюю панель надо тщательно отшлифовать. Для этого соберём небольшое приспособление.
Панель закрепляется на основании из ДСП, сбоку прикручивается угольник – он служит направляющей. Полоска наждачной бумаги со средней зернистостью прикрепляется к отрезку того же ДСП. Наждачная бумага перемещается вдоль панели и одновременно прижимается к направляющей. Это позволит получить параллельные риски на панели.
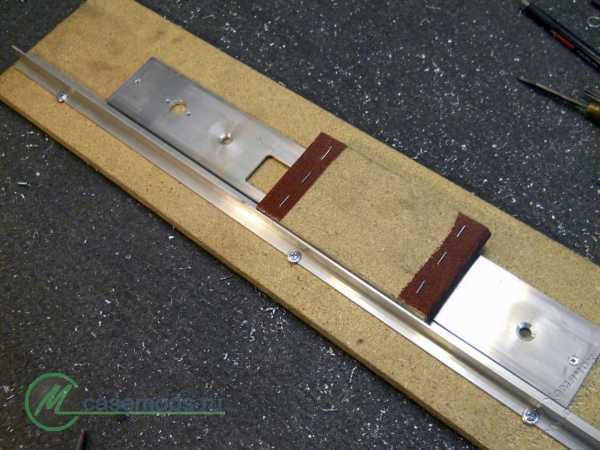
При обработке панель надо обильно поливать керосином. Его можно налить в распылитель, будет очень удобно. Панель должна быть всегда влажной. Не трите на сухую! Могут остаться трудноустранимые дефекты.
Через час можно будет полюбоваться на результаты.
Ручку громкости можно отполировать при помощи дрели.
Осталось дело за малым – вырезать стёкла для отделки корпуса. Я применил для этого зеркало серого цвета. Самое простое – заказать всё это в зеркальной мастерской, но можно сделать самому. Отрезать стекло – не проблема, а вот обработать кромки – это надо постараться. Обработка производится наждачной бумагой с водой. Постепенно уменьшая номера, можно добиться почти идеальной полировки. Но можно остановиться и на ровной матовой поверхности.
Боковые полоски стекла приклеиваются к корпусу при помощи аквариумного силикона.
Стекло в углубление вклеивается при помощи эпоксидного клея. После отвердения, излишки клея удаляются острым лезвием.
Собираем индикатор. Картинка для шильдика рисуется в любом графическом редакторе и печатается на самолеящейся плёнке белого цвета.
Ещё хорошо бы заказать у токаря декоративные подкладки под винты, они придадут профессиональный вид усилителю.
Сам корпус покрывается чёрной краской из баллончика, но это тоже не является необходимостью – каркас почти не виден. Если крышка корпуса сделана из стекла, кстати, хорошие результаты даёт обычное зеркало, в ней надо просверлить отверстия. Я их делал при помощи трубчатого сверла. Сначала до половины толщины с обратной стороны зеркала…
А потом с лицевой. Если делать наоборот, то не будет видно, где сверлить, а насквозь сверлить не советую – в этом случае сколы неизбежны.
Теперь берём светодиод красного цвета и диаметром три миллиметра. В ручке громкости сверлится отверстие с лицевой стороны диаметром три миллиметра, а с обратной, почти до конца, надо рассверлить его сверлом четыре миллиметра. К светодиоду припаивается резистор, и провода изолируются трубочками. Желательно применить провод марки МГТФ.
Полученная конструкция вставляется в отверстие и закрепляется каплей клея.
Рукоятка ставится на место, а провода пропускаются в щель между панелью и осью.Провода от светодиода подключаются к питающему напряжению.
Вот теперь всё! Осталось закрепить верхнюю крышку. Под винтики тоже желательно подложить декоративные подкладки. Но можно применить винтики чёрного цвета.
Завершающим этапом делаем надписи на передней панели. Самый простой вариант – напечатать их на прозрачной самоклеящейся плёнке. Я именно так и поступил.
Вот, что у вас должно было получиться в итоге.
Не хвастаясь скажу, что у меня на эту работу ушло шестнадцать часов. Так что этот усилитель вполне возможно построить за выходные дни. Успеха!
cxo.lv
Изготовление корпуса и передней панели для самодельного усилителя Phoenix P-400
В данной публикации будет идти речь об изготовлении передней панели к самодельному усилителю, а также немного расскажу как я планировал корпус усилителя. Поведаю вам о простом способе нанесения надписей на металлическую поверхность передней панели, а также о других полезностях при планировании и изготовлении корпуса для самодельного УМЗЧ.
Содержание:
- Корпус для усилителя мощности
- Планировка передней панели усилителя
- Нанесение надписей на переднюю панель УМЗЧ
- Лакирование и панель индикации
- Верхняя крышка для корпуса усилителя
- Последние штрихи и некоторые заметки
- Результат
- Заключение
Корпус для усилителя мощности
Прежде чем приступить к проектированию корпуса усилителя мне нужно было решить задачу с выбором радиаторов для охлаждения мощных транзисторов КТ825+КТ827. Установленные радиаторы займут достаточно большую площадь в корпусе или на корпусе УМЗЧ. На каждые два канала УМЗЧ приходится по 4 транзистора — в сумме 8 транзисторов, нужно распределить их по радиаторам.
Сначала думал установить все транзисторы на два длинных радиатора — по 4 транзистора на каждый, которые бы выступали в роли боковых частей корпуса, но радиаторного профиля нужной высоты и площади теплоотдачи я не нашел.
После копания в домашнем хламе были найдены компактные радиаторы и с достаточно большой площадью рассеивания тепла, на которых били установлены старые транзисторы КТ805А в металлическом корпусе.
Рис. 1. Радиаторы от транзисторов КТ805А.
Немного прикинув расположение этих радиаторов по сторонам уже думал отказаться от затеи их использования, тем более что будет немало возни с креплением транзисторов КТ825, КТ827 в корпусе TO-3, придется сверлить отверстия и снимать небольшой слой металла напильником или фрезой.
В это же время в гости ко мне в комнату зашел отец, немного побеседовав на тему корпуса для УНЧ я решил все же применить эти радиаторы.
Все транзисторы были установлены на 8 радиаторов, для крепления использовался изолированный монтаж со слюдой в качестве диэлектрика и проводника тепла, также в ход пустил белую термопасту от тех же КТ805А которые были установлены на радиаторах изначально.
Об изолированном способе установки транзисторов в корпусе TO-3 на радиаторы я рассказывал раньше в статье по изготовлению схемы УМЗЧ на TDA7250.
Имея в наличии радиаторы и поигравшись немножко с их расположением я принялся чертить план корпуса усилителя в AutoCAD (сейчас для черчения использую свободный LibreCAD).
Полезно знать: для преобразования файлов формата *.dwg для AutoCAD в формат *.dxf для LibreCAD и других программ, достаточно хорошо себя зарекомендовала программа-конвертер под названием «Teigha File Converter», которая доступна в свободном доступе под Windows, Linux, Mac OS X и Android.
Рис. 2. План корпуса для самодельного усилителя в AutoCAD.
По ширине я старался сделать корпус усилителя таким же как и многие отечественные УНЧ, к примеру как у Radiotehnika-U101. Таким образом ширина задней панели, на которой будут крепиться разъемы и клемы усилителя, получилась 150мм.
Длина корпуса усилителя получилась равной длине трех радиаторов + толщина передней панели. По середине корпуса будет установлен тороидальный трансформатор, а дальше придумаю как разместить всю остальную электронику.
На задней панели должны размещаться:
- 4 разъема RCA (тюльпан) для подключения источников сигнала;
- 4 держателя под предохранители для АС + 1 держатель предохранителя питания 220В;
- 1 разъем IEC (как у БП компьютера) для подключения питания 220В;
- 2 клеммника WP4-7 для подключения 4х акустических систем;
- 1 COM-порт, на случай как найду время сделать управление через компьютер.
Проектировал размещение компонентов на задней панели по старинке — на листе бумаги в клеточку:
Рис. 3. План размещения разъемов на задней панели усилителя мощности, нарисованный на листе бумаги.
Рис. 4. Готовая задняя панель для самодельного усилителя мощности.
Все разъемы и держатели для предохранителей удалось разместить достаточно компактно и удобно. Перед их креплением панель с вырезанными отверстиями была покрашена в белый цвет при помощи аэрозольного баллончика с краской.
Для дна корпуса усилителя была вырезана пластина из алюминия толщиной примерно 2мм и по размерам получившегося прямоугольника из радиаторов и задней панели.
Для будущей передней панели усилителя мощности был вырезан кусок дюралюминия толщиной 5мм, высотой 75мм и шириной 450мм.
Рис. 5. Заготовки для корпуса усилителя — радиаторы, задняя панель, днище и пластина для передней панели.
Рис. 6. Корпус самодельного УМЗЧ в сборе.
Планировка передней панели усилителя
Имея почти готовый корпус усилителя и пластину под переднюю панель я начал планировку последней, начертил что и как должно размещаться и в каких размерах.
На передней панели располагаются:
- Индикаторы выходной мощности — 4 ряда по 9 светодиодов (5мм) в каждом;
- Кнопка включения питания;
- Двухцветный светодиод (5мм) — индикатор питания и ждущего режима;
- 4 переключателя ПР 2-10, каждый на 10 позиций — регуляторы громкости для каждого из каналов;
- 2 переключателя для возможности отключить любую из двух пар каналов;
- Гнездо под джек для наушников;
- Панель индикации — температуры компонентов, режимы, перегрузка, состояние вентиляторов.
Рис. 7. План передней панели для самодельного усилителя мощности Phoenix P-400.
Рис. 8. План передней панели усилителя с раскраской и без указания размеров (без гнезда для наушников).
Мне понравилась такая планировка и я решил приступить к ее реализации, осталось лишь подобавлять некоторые надписи и посмотреть как все будет выглядеть:
Рис. 9. План передней панели усилителя с надписями для элементов управления.
Изготовление передней панели усилителя
Имея четкий план и заготовку можно приступать к работе. При помощи наждачки+усилия+терпения с дюралюминиевой панели были убраны все впадины, остатки краски и последствия небольшого окисления.
При устранении дефектов поверхности я выполнял движения наждачной бумагой так, как это было удобно, то есть в разнобой, в разные направления и углы. По завершению и после осмотра было принято решение выполнить дополнительную (чистовую) шлифовку, которая исправит косметический вид пластины.
Для этого нужно было многократно пройтись наждачной бумагой вдоль всей панели, ровно и в одном направлении (к примеру с лева направо). После такой шлифовки пластина выглядела достаточно аккуратно и симпатично.
После, в соответствии с чертежом который был нарисован выше, начал разметку мест для сверления отверстий под элементы управления и индикации при помощи линейки+угольника+циркуля+карандаша. Перед высверливанием, места для отверстий не помешает наметить керном.
Отверстия под светодиоды делались сверлом диаметром 5мм, как после этого показала практика пришлось лишь несколько отверстий подвести под нужный диаметр светодиодов при помощи маленького круглого надфиля.
Отверстия под переключатели (питание и регуляторы), кнопку и джек высверливались сверлом максимально подходящего диаметра, если же такое не найти — не беда, сойдет и поменьше, потом можно будет довести диаметр до нужного значения при помощи круглого напильника.
Оставалось еще одно непростое испытание — изготовить прямоугольное отверстие размерами 136х45мм для панели индикации усилителя. Взвесив выбор подручных средств что есть в наличии, выделил для себя несколько вариантов решения:
- Сверлим по всему периметру прямоугольника одно возле другого отверстия диаметром примерно 5мм. Потом избавляемся от перегородок между отверстиями и изымаем вырезанный кусок пластины. Перерезать перегородки можно при помощи надфиля или же лобзика (заранее запаситесь пилочками). После, при помощи напильников убираем все неровности и максимально выравниваем форму вырезанного прямоугольника.
- Этот вариант пришел в голову после анализа предыдущего. Суть его проста — сверлим одно отверстие, к примеру в углу прямоугольника, собираем все свое терпение, запускаем иглу лобзика в высверленное отверстие и начинаем вырезать прямоугольник по начерченному контуру.
Оценив количество возни в первом варианте и во втором я принял решение что второй вариант проще и позволит получить более аккуратный результат. Приступая я даже не подозревал что меня ждут около двух часов напряженной работы, около десятка поломанных пилочек для лобзика и несколько мозолей на руках…желание получить нужный результат помогло добиться поставленной цели!
Все получилось очень аккуратно и пришлось лишь немножко подправить весь периметр прямоугольника при помощи плоского напильника. Не могу никому советовать данный вариант, поскольку резать лобзиком металл диаметром 5мм — занятие очень непростое, возможно даже немного сумасшедшее. Что было на то время у меня под рукой, то и использовал, сейчас бы точно таким не занимался — сходил бы куда-то на завод и там бы все сделали гораздо проще.
Нанесение надписей на переднюю панель УМЗЧ
Думаю что этот пункт будет интересен очень многим, особенно тем кто мастерит различные корпуса для устройств из металла, не только усилители мощности.
Полагаю что многие из вас знакомы или же хоть раз где-то слышали о таком явлении как Лазерно Утюжная Технология (или просто в народе — ЛУТ), применяемая для изготовления печатных плат в домашних условиях.
Я также в свое время слышал о ней, но еще даже не опробовав ее для изготовления печатных плат (всегда по старинке трафарет рисовал вручную на листе бумаги + шприц с лаком для нанесения на текстолит) принялся использовать ее для нанесения надписей на металл.
Суть методологии ЛУТ очень проста, сейчас подробно распишу как я наносил надписи на пластину из дюралюминию для передней панели своего самодельного усилителя мощности звуковой частоты.
Зачищаем металл мелкозернистой наждачной бумагой, добиваемся чтобы поверхность была ровной и гладкой (это я уже делал, описано выше). Очищаем и обезжириваем поверхность пластины при помощи тампона из ватки, смоченного в растворитель.
Распечатываем на ЛАЗЕРНОМ принтере нужный трафарет со всеми нужными надписями и в нескольких копиях на странице извлеченной из прочного глянцевого журнала.
Печать нужно выполнять в зеркальном отображении, чтобы после перебивки надписи на металле были в правильном положении. Отобразить изображение можно в любом графическом редакторе или же при помощи программы в которой чертили рисунки.
Рис. 10. Трафарет с надписями для передней панели моего усилителя.
Если напечатанный рисунок достаточно большой по размеру, то возможно что лучше его разрезать на части размером поменьше. Я именно так и сделал — отдельно вырезал трафареты с надписями сверху, с рисунками для каждого из регуляторов громкости, наушников…
Мелкими частями трафареты намного удобнее центрировать, особенно те что с круговыми отверстиями. Для этого внутреннюю часть бумаги подготовленного кусочка трафарета можно надрезать от центра к краям и получившиеся лепесточки вдавить в отверстие, тем самым надежно отцентрировав трафарет.
Рис. 11. Напечатанные на журнальном листе бумаги и в зеркальном отображении надписи для передней панели УМЗЧ.
Разогреваем утюг. Я использовал еще советский со сплошной массивной подошвой из металла, остывает она медленно и соответственно накапливает достаточно тепла для теплопередачи.
Пластину из металла нагреваем утюгом до температуры немного ниже максимальной температуры утюга, это делается «на глаз», к тому же пластина остывает достаточно быстро — можно разогреть до максимума и после сделать небольшую паузу перед следующим шагом.
В моем случае пластина достаточно длинная, поэтому я переносил надписи по порядку: нагревал сначала одну сторону пластины, переносил надписи, потом приступал к надписям посередине и грел середину пластины, а потом уже оставшуюся сторону.
Процесс переноса надписей очень прост — прикладываем трафарет, центрируем и позиционируем как нужно, потом прикладываем сверху на трафарет подошву утюга и держим так секунд 10, после дав остыть секунд 10 начинаем аккуратно как бы «втирать» трафарет по всей площади.
Приклеив таким способом несколько трафаретов можно перейти к следующему этапу. Можно конечно приклеить все трафареты сразу, но это уже как кому удобнее, попробуете и определите для себя подходящий вариант.
Ищем емкость с размерами, достаточными чтобы погрузить в него изготавливаемую пластину, можно также использовать ванну.
Набираем в нее теплую воду с температурой примерно 30-35 градусов по Цельсию. Аккуратно погружаем в теплую воду нашу пластину с приклеенными трафаретами.
Ждем примерно 10-15 минут чтобы бумага полностью размокла и легко отслоилась от металла, отделяем ее и протираем панель с надписями отрезком сухого полотна.
Ожидаем немного пока надписи на панели просохнут — на них станут видны тонкие слои белых волокон — это остатки от бумаги. Убираем эти волокна при помощи ватки смоченной в спирт, делаем это аккуратно и с небольшим усилием.
Повторяем процесс обезжиривания металла на следующем участке где нужно клеить надписи (мало ли что, руками все-таки пачкаем), греем утюгом, кладем трафарет, греем его, а потом втираем, мочим в воде, протираем…повторяем пока все надписи не будут нанесены.
Все, надписи готовы!
Может случиться так, что с первого раза получить целые и качественные надписи не получится — не отчаивайтесь, пробуйте и экспериментируйте.
Я распечатывал трафареты на листах бумаги из разных журналов, только два типа бумаги дали хороший результат — они хорошо размокали и отслаивались от перенесенного на металл тонера.
Лакирование и панель индикации
После нанесения всех надписей на металл, передняя панель была полакирована при помощи аэрозольного баллончика с прозрачным лаком. Лакировал я ее несколько раз на протяжении двух дней. Дождавшись пока все хорошо высохнет я принялся за изготовление табла с элементами индикации.
Выше я привел план передней панели и на ней уже изображены светодиоды индикации, а также цифровые индикаторы, по середине есть площадка для нанесения рисунка — небольшого Феникса.
В принципе можно сделать непрозрачную панельку и все разместить как есть, но я захотел чего-то более интересного — Феникс будет светиться, а вместо торчащих светодиодов будут светиться надписи!
Как такое реализовать? — напечатать подкладку из пленки на которой будет прозрачными только надписи, отверстия под цифровые индикаторы и по середине изображен полупрозрачный рисунок феникса.
Основу трафарета начертил в автокаде, потом конвертировал в рисунок и открыв его в Photoshop добавил посередине рисунок Феникса, а еще добавил маленькие картинки-черепушки, которые будут светиться красным при превышении максимально выставленной мощности (эти светодиоды подключены к каждому 10-му каналу светодиодных индикаторов выходной мощности).
Рис. 12. Трафарет для панели индикации самодельного усилителя.
Иконки с восклицательным знаком «!» будут подсвечиваться при срабатывании защиты АС, а также при старте усилителя (задержка включения АС и подавление щелчка).
Надписи «On» будут светиться зеленым если соответствующие каждой стороне пары каналов УМЗЧ включены при помощи выключателей. Надпись «Fan» будет светиться когда начнут работать вентиляторы охлаждения транзисторов выходных каскадов УМЗЧ. Иконки с индексом «t» подсвечиваются постоянно под каждым из цифровых сегментов, которые отображают уровень температуры от 9 до 0:
- Для транзисторов УМЗЧ левой пары каналов;
- Для тороидального трансформатора;
- Для шасси усилителя;
- Для транзисторов УМЗЧ правой пары каналов.
Решение с уровнями температур смотрится немного запутанно, но тем не менее достаточно информативно. Сейчас если бы мастерил подобный УМЗЧ то индикацию сделал бы с нормальными термометрами и на микроконтроллерах, а на то время что пришло в голову из бюджетных и доступных вариантов — то и реализовал.
Сохранив рисунок в файл формата PDF (Portable Document Format от Adobe) я отправился в типографию, где мне за несколько часов предоставили готовый результат в нескольких экземплярах на прозрачной пленке.
Рис. 13. Напечатанный на пленке трафарет для панели индикации усилителя.
Панель индикации будет спрятана за прямоугольной пластиной из органического стекла (оргстекла) толщиной 3мм, которая будет помещена в прямоугольное отверстие передней панели усилителя. За этой пластиной будет помещен трафарет, распечатанный на пленке, а уже за ним прикручена плата индикации с подстветкой Феникса, индикаторами и светодиодами.
Все компоненты индикации должны размещаться на печатной плате, которую нужно спроектировать под изготовленный трафарет. Для проектирования такой печатной платы на листе бумаги в клеточку, я распечатал трафарет панели индикации, приложил его на лист бу
ph0en1x.net
Корпус усилителя мощности своими руками
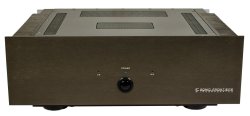
Приличный корпус для усилителя сделать можно. Своими руками, с помощью простейших ручных инструментов. Применяя детали из готовых устройств с минимальными переделками.
Никаких новейших технологий и станков, только желание и немного умения. Железяка старая, делал 10-15 лет назад, процесс не фотографировал, но взамен фотографиям нарисовал рисунки. Делал около полугода вечерами, частично на работе, частично дома.
И одну неделю вечерами на кухне без уборки и наведения порядка, когда жена с дочкой были в отъезде. За эту неделю очень существенно продвинулся, поэтому и раскрываю тайну.
Но Вы никому не говорите!
Даже и не помню, как я на такое повёлся, может быть это была зависть к красивой аппаратуре из журналов, может вид имеющихся самоделок уже надоел, не знаю. Сейчас бы я на такое не решился, наверное, все-таки работа приличная и кропотливая.
Но глядя сейчас на усилитель, я рад, что тогда не спасовал, получилось недурно, внешним видом доволен.
Короче так или иначе, а надо было строить. Стройку начал с обдумывания назначения, компоновки и естественно внешнего вида в общем. Строить собрался именно усилитель мощности, предварительный на тот момент у меня был, был в отдельном (деревянно-пластмассовом) корпусе.
Весь этот дизайн внешнего вида, компоновка напрямую зависели от имеющихся или потенциально имеющихся заготовок и деталей. Поэтому сперва прикинул, что у меня есть, что нужно добыть, и как все это соединить, чтобы получить то, что хочу.
Ну раз усилитель мощности, значит на передней панели ничего можно не ставить, кроме разве только сетевой кнопки и парочки каких-нибудь индикаторов включения/выключения. Это радует-сверлить много отверстий и придумывать где их размещать не нужно.
Я выбрал дизайн, где сетевая кнопка находиться по центру панели. Соответственно и установить я ее собирался сразу за передней панелью, а сетевой провод до кнопки провести через весь усилитель.
Как раз мне товарищ презентовал алюминиевый профиль, достаточно широкий, чтобы из него можно было сделать высокую ПП (переднюю панель).Еще одним достоинством такого профиля была возможность прикрепить его к остальному корпусу не портя само лицо усилителя всякими винтами и саморезами.Т.е почти заводкая ПП.
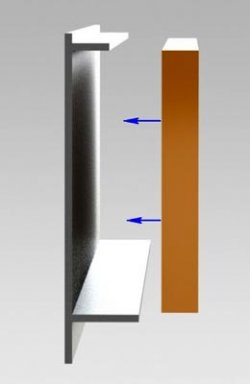
К передней панели у меня крепятся кой-какие детали, и я для облегчения процесса крепежа,
между ребрами поставил деревянную панель. Очень удобно.
Добыл несколько радиаторов, у которых сразу отрезал ножёвкой все рёбра с одной стороны, и немного привёл их в нормальный вид: подчистил, притупил кромки и снял фаски. Сторону на которую надо крепить активные элементы отшлифовал более тщательно. Шлифовать до ровности не обязательно все, можно только то место на которое потом станут или МС или транзисторы. Потом покрасил (но только снаружи).
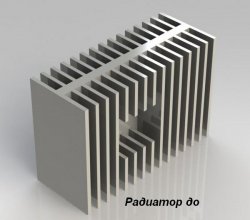

Длины радиаторов не хватило на всю глубину корпуса, пришлось нарастить еще куском .И все. радиаторы кончились, а надо еще немного, около 60 мм.
Ну и фиг с ним, еще радиаторы искать не стал, это место закрыл деревянной покрашенной вставкой.
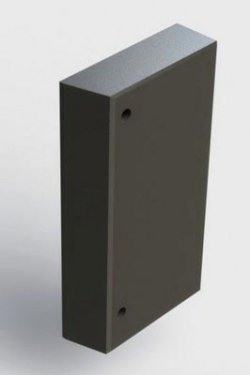
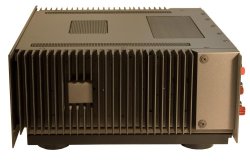
Эти все части радиаторов и вставка скреплены сверху (изнутри усилителя) алюминиевым уголком.
В принципе вот и готовые боковые стенки. А снизу вся эта конструкция прикручивается к шасси.
А шасси служит железяка (эпу) от вертушки вега 110.Она же и определила глубину усилителя. Железо там хорошее, в меру толстое, края загнуты (отбортованы), то что надо.
Если прикрепить радиаторы к шасси, уже получается почти макет корпуса, на который можно все ставить и испытывать усилитель.
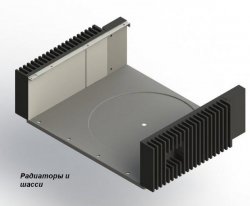
Что ещё остается для полноценного корпуса? Задняя стенка (в которой нужно делать много всяких отверстий и креплений), верхняя крышка (с отверстиями для вентиляции), ну и как то надо облагородить низ усилителя-сделать днище и поставить усилок на ножки.
Само шасси незаконченная конструкция, крепить ноги и днище к нему неудобно. Да и внешний вид «голимый» Пришлось сделать рамку из дерева определенного профиля.
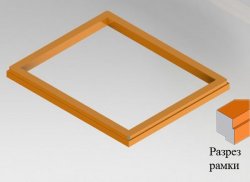
Рамка вставляется в шасси снизу, а к низу самой рамки в четверть крепиться пластмассовое днище.
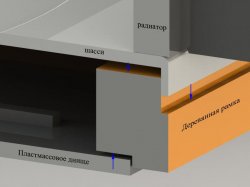
Днище прекрасно получилось из пластикового днища той же Веги 110.
Заднюю стенку и крышку пришлось вырезать из цельного куска какого-то дюралюминия. Поцарапанного, и местами с выбоинами. Пришлось попотеть… Ножовка, цикля, напильники, наждачная бумага-все пошло в ход.
Крепление частей в основном винтами и саморезами: радиаторы на шасси винтами (в радиаторах сверлил отверстия и нарезал резьбу, потом снизу винты М5),
Остальное по разному, где винты, где саморезы.
Ножки привинчены к пластиковому днищу изнутри, а на металлическом шасси снизу, в тех местах, где установлены ножки, приклеены брусочки. Чтобы потом, в готовом виде днище не прогибалось под тяжестью корпуса.
Днище крепиться к рамке саморезами. Сама рамка уже закреплена на шасси.
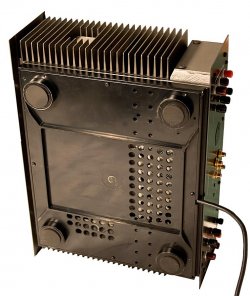
Изначально в крышке просверлил для вентиляции отверстия. По памяти, то ли 10, то ли 8 мм диаметром. Аккуратными рядами. Это уже потом, через полгода сделал сетки.
Вот как раз в тех местах, где сетки и были отверстия.
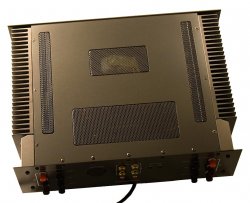
Хотелось избавиться от видимого крепежа и сверху, но не вышло-ничего не придумал.
Поэтому помучился немного с подгонкой отверстий. Ручной дрелью, аккуратно, по чуть чуть подгонял фаску по глубине, чтобы шляпки саморезов топились одинаково и заподлицо.
Шляпки у саморезов полукруглые. В общем старался, чтобы выглядело по «заводскому».
Стык ПП и крышки получился без саморезов. Там в ПП есть паз, куда классненько так вставилась крышка.
Ну… с заднее панелью вроде все ясно из фото.
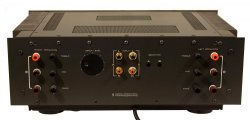
Все стандартно, только ручки «input level» сразу не было. 4-х разъёмов входов и кнопок рядом с ними тоже. Это уже потом. Такой вот апгрейд. Чтобы громкость регулировать без предвара, пока предвар, ну скажем перебирается или перепаивается. Заодно появилась возможность оперативно сравнить звук с предварительным и напрямую.
Давно уже собираюсь заменить колоночные клеммы на более кошерные, но как то недосуг, хотя все есть.
Покраска деталей более менее стандартная, технологий особо я не знал, как то интуитивно покрасил. Радиаторы, красил на «горячую-горячую» — на нагретый радиатор наносил нитроэмаль.
Так прочнее держится. ПП крышку и остальные аллюминиевые части загрунтовал перед покраской
порошком, разведенным в растворителе. Порошок- для порошковой окраски корпусов СВЧ печей.
Если грубо не скрести и не бить, пока все держится.
Покрашено все в темно серый цвет. Смесь черной нитроэмали+ немного аллюминиевой пудры+ еще чего-то цветного для придания нужного оттенка.
Фото внутренностей.
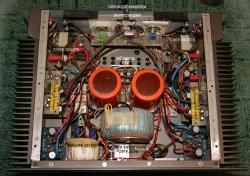
В стойке
Предусилитель, УМЗЧ, источники.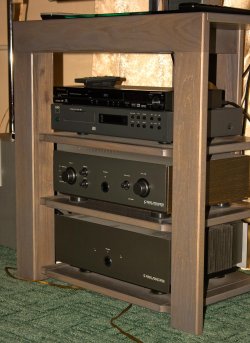
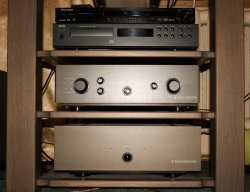
Вот вроде и все.
Поскриптум: написано естественно не все, многих мелочей нет. Чтобы написать все полностью нужно
намного больше писанины, с эмоциями, переживаниями…много технических моментов пропущено. Мелочевки. Но основное здесь есть.
Самым простым оказалось вставить подготовленную статью в редактор портала. Ушло от силы 15 минут. А этого как раз я и боялся больше всего… Самым сложным — написать статью.
Лично мне с художественной стороны не очень нравиться. Сужу по факту. Но уж как есть. По другому не смог придумать.
Если вы это читаете, значит прочли. Спасибо!
Дмитрий (Dimonos)
г.Минск
Мне 48 лет паяльник в руки взял еще в школе, в году где то 1978, Начал с акустики. Самоучка-радиотехнического образования нет.Сначала занимался довольно активно,теперь не хватает времени. Сконструировал и изготовил несколько удачных АС (из 10-15 неудачных). Затем пошли кассетные магнитофоны,автомагнитолы,ремонт и настройка акустики и их совместной «жизни» с усилителями.
В данный момент активно «физически» «радио» не занимаюсь, только теория, проекты. Помогаю друзьям и товарищам.
Измерительной аппаратуры нет (только осцилограф и компьютер).
Увлекаюсь… книги разного направления и тематики: фантастика, детективы… Ну не знаю, что сказать.
Уделяю особое внимание доработке (доводке конструкций).
Никакой комерцией по радио не занимался.
Пришел, наверное, чтобы поделиться чем то удачным и приобрести больше знаний и опыта.
datagor.ru
Мультиобзор. Корпус для аудио усилителя мощности Дорофеева
$11,53+GBP 4.70+1000 р.+160 р.+633 р.+EUR 3.40 +$9.55Некоторое время назад делал обзор радиоконструктора УНЧ Дорофеева с импульсным блоком питания. Сегодня обзор про изготовление корпуса для этого УНЧ. Основные детали покупались на ebay — на этой площадке всякая мелочь обычно чуть дешевле, чем на других площадках, оплата палкой. Ссылка шапке обзора — селектор каналов, который применил в конструкции. На другие части конструкции — ссылки внутри обзора.
Поначалу раздумывал: стоит ли писать обзор на изготовление корпуса для УНЧ. Хотя процесс изготовления фотографировал. Но тут на дня появился обзор про корпус УНЧ. Решил написать обзор про свой корпус.
Введение
Корпус для самоделок можно:
1. Сделать «с нуля» самому — затратный по времени, материалам и инструментам процесс. Плюс надо обладать слесарно-столярно-малярными навыками на достаточно высоком уровне.
2. Купить подходящий корпус в Китае/России/где-то еще. Получаем качественный профессиональный корпус. Слесарные навыки ограничиваются владением дрелью для сверления отверстий под крепление плат. Правда есть риск получить стандартный корпус «как у всех»
3. Найти «устройство-донора» и встроить туда свою самоделку. Я решил пойти по этому пути. Путь оказался не такой простой, как может показаться на первый взгляд.
Донор
Старый VHS видеомагнитофон. От ждал кладовке своего часа, чтобы послужить корпусом для какого-нибудь устройства.
Я разобрал старый аппарат, вынул всю электронику.
Минусы этого корпуса:
1. Надпись «Хитачи» на верху корпуса и отсутствие вентиляция. Для УНЧ лучше, чтобы корпус был вентилируемым.
2. Сложная передняя панель — много вырезов
3. Пластиковая нижняя часть корпуса. Избегайте таких корпусов! Пластик не такой прочный, как металлический. Нет свойств «экрана». Лучше, чтобы корпус был из металла полностью.
4. Много вспомогательных пластиковых стоек — срезал их дремелем.
Итог — будет много сложностей с переделкой корпуса.
Верхняя крышка
Сначала хотел просветлить в верхней крышке МНОГО вентиляционных отверстий. Напечатал шаблон.
Начал кернить отверстия. Терпения хватило на несколько рядов. Потом попробовал просверлить отверстия. На 10-м отверстии решил забросить это дело. Надо искать другой вариант.
Утром отвозил мусор из дома на помойку. Увидел бомжа, который крутил в руках корпус от старого компьютера. Ура! Боковая стенка с кучей для вентиляции отверстий!!! подошел к бомжу. Переговоры. «Очень нужно для дела!» Бомж отдал свою добычу. Сказав спасибо и пожелав удачного дня, довольный погрузил находку в машину. Вырезал дремелем нужный кусок металла и окно в верхней панели. Закрепил винтами М3 с круглыми головками, очистил от старой краски:
Длинные винты срезал дремелем:
Есть проблема — неровности:
Залил неровности эпоксидной смолой, отшлифовал наждачной бумагой и покрасил крышку черной краской из баллончика (160 р.). Получилось так:
Задняя панель
Проблема готовых корпусов — лишние отверстия в задней панели. В моем случае эта панель сделана из пластика. Лишнее заклеил черным пластиком от папки для бумаг и клеем «Момент». Просверлил отверстия для входов усилителя, установил гнездо питания и терминалы для акустики:
Терминалы для акустики покупал на ebay за GBP 4.70 (400 р.)
Прислали терминалы с более длинными винтами, чем на странице товара. Но, как потом оказалось — это к лучшему. Проще закрепить на терминалах выходные цепи Буше и Зобеля.
Передняя панель
Самая важная часть усилителя. Ее видит пользователь. Не зря ее называют лицевой панелью.
В моем случае панель от видеомагнитофона имеет сложный рельеф:
С обратной стороны заклеил все отверстия бумагой, приклеил бортик из картона и залил все сверху эпоксидной смолой. На эпоксидку для УНЧ ушло около около 1000 р. Отшлифовал переднюю и боковые части панели:
Лицевую панель вырезал из листа алюминия толщиной 1.2 мм — покупал в Леруа за 633 р.. Толще заготовку из алюминия нужного размера и по разумной цене и размерам в нашей деревне не нашел. Отполировал наждачной бумагой:
Нанес надписи с помощью ЛУТ-а. Панель приклеил эпоксидкой к подготовленной передней части. Боковые части панели заклеил черной самоклеющейся пленкой. Получилось так:
Надписи:
Такая проблема — сделать красивые надписи на самодельную аппаратуру. Есть разные способы:
1. Трафареты, перманентный маркер, гравировка или переводной шрифт — устаревший способ. Нужно иметь хороший скил при использовании этих способов. Большая вероятность, что получиться по-колхозному.
2. «Переводные картинки». Покупается специальная бумага для переводных картинок. На ней печатаются на лазерном принтере надписи. Надписи вырезаются, кладутся в теплую воду и потом переводиться надпись на панель. Бумага вынимается, а надпись на панели остается. Способ отличный. Но такая бумага стоит очень дорого и в нашей деревне ее не продают.
3. ЛУТ. Технология широко известна для изготовления для печатных плат для самодельной электроники. Для нанесения надписей на лицевую панель тоже можно использовать. Важен выбор бумаги для термопереноса. Лучше использовать китайскую бумагу для ЛУТ c ebay:
Эта бумага хороша тем, что поле переноса остается черная надпись без белого налета. Если использовать, например, глянцевую бумагу для струйного принтера, то после удаления бумаги, останутся белые следы от бумажной основы. Для печатной платы это не существенно. В случае панели будет некрасиво. Еще из-за листа белой бумаги сверху бумаги с надписью (а его необходимо подкладывать сверху — иначе можно поцарапать панель утюгом при переносе), тяжело правильно спозиционировать надписи.
Печатаем лазерным принтером на глянцевой стороне зеркально отображение надписи. Чистим, обезжириваем панель. Прикладываем напечатанный лист или вырезанные надписи к панели, чтобы не поцарапать панель — лист белой бумаги сверху и аккуратно переносим утюгом, гладя сверху. Когда все остынет, замочить в теплой воде и удалить желтую основу. Если получилось криво, то смыть надписи ацетоном и попробовать еще раз. Панель сверху покрыть бесцветным лаком, чтобы надписи не стирались. Если панель целиком помещается на лист А4, то лучше сразу все напечатать на одном листе и перенести все надписи за один раз.
Использовал этот способ в первом варианте лицевой панели. Перенес надписи на алюминиевую заготовку панели, покрыл бесцветным лаком и приклеил панель эпоксидным клеем на пластиковую переднюю часть от бывшего видеомагнитофона. Получилось так после приклейки алюминиевой панели к основе:
Как видно — способ жизненный и достаточно простой.
К сожалению, в процессе сборки испортил переднюю панель. Пришлось все переделывать. Второй раз перенести надписи на панель с помощью утюга уже невозможно. Эпоксидка не выдержит температуры утюга и пластик основы может поплавиться. Защистил, все заполировал. Для надписей использовал четвертый способ:
4. Самоклеющаюся бумага для принтера:
Бумага существует для разных типов принтеров. Я покупал для лазерного принтера. У меня такой. Такая бумага бывает с прозрачной и с белой основой. Прозрачная — для надписей на светлом фоне, куда мы будем клеить. Белая — для темного фона. Напечатал надписи. На всякий случай, сделал несколько копий надписей — если криво приклею. Далее вырезаю надписи и наклеиваю на нужные места.
Скальпелем отделяю основу и приклеиваю на нужные места панели. Покрыл бесцветным лаком сверху.
Плюсы способа — просто, недорого и можно наклеивать на готовые устройства. Если есть желание, то можно поменять место нанесения надписи. Минус способа — если присмотреться, то видно что наклейка. Шаловливые ручки могут отодрать надпись.
Нижняя часть
Силовая основа конструкции. У меня она пластиковая. Можно все разместить на шасси (лист алюминия, например). Но это не мой способ. В этом случае конструция не поместится в корпус из-за лишнего расстояния между шасси и и нижней частью корпуса. Проблема вентиляции.
Срезал дремелем все лишнее. Просверлил отверстия для плат, ножек, вентиляцию и вентиляторы:
Ножки для корпуса усилителя покупал на али в известном магазине Aiyima. Взял самые большие по диаметру:
Ножки пластиковые. Амортизатор из резины. Сверху покрыто фольгой или напылением пластик. Никакого алюминия выточенного на токарном станке нет и в помине.
Части усилителя
Корпус в разборе:
Электроника и крепеж:
Основная плата УНЧ и блока питания:
Вспомогательный блок питания для вентиляторов, защиты акустической системы и селектора каналов. Сделал сам лутом и детали из оффлайна:
Селектор каналов на три входа — покупал на ebay $11.53:
Селектор питается от ПОСТОЯННОГО напряжения 12В. Переключатель — тумблер на три положения. Среднее положение — все отключено, два остальных положения — соединяют центральный вывод тумблера двумя крайними выводами.
Я выпаял тумблер, на проводами удлинил выводы, установил разъем для удобства разборки и приклеил тумблер селектора на переднюю панель эпоксидкой.
Защита акустической системы от постоянного напряжения на выходу УНЧ — покупал на ebay за EUR 3.40 (250 р.)
Защита работает от переменного напряжения 12 В. Основа схемы — чип UPC1237. Конструкция предназначена для установки на терминалы акустической системы. Специально такую брал. Правда перерезал дорожки к минусовым терминалам — провода от этих терминалов провел прямо к общей точке соединения земель усилителя — конденсаторы фильтра блока питания усилителя. Минус этой защиты — долго подключает акустику к выходу УНЧ. примерно через 20 секунд после включения питания УНЧ.
Вентиляторы для охлаждения выходных транзисторов УНЧ на радиаторах нужны в моей конструкции из-за небольшого размера радиаторов. Большего размера радиаторы не помещались в корпус. Купил 4 вентилятора на 12 Вольт размером 5 на 5 см высотой 6 мм. Брал на ebay. Товар не продается теперь. Похожие не нашел. Но много аналогичных. В оффлайне стоили такие в три раза дороже.
Установленные вентиляторы:
Удлинитель регулятора громкости покупал на ebay за $9.55:
Состоит из трубки, крепежа на переднюю панель, держатель для переменного резистора регулятора громкости (РГ) и переходная муфта. Трубку я укоротил под нужную длину. Стойку РГ я сам сделал. Но использовал в итоге из этого набора. Оказалась удобнее.
Смонтировал все в корпус — провода стяжками еще не закрепил:
Провод к верхней крышке ведет в точку «подключение экрана к общему проводу усилителя».
На радиаторы установил термовключатели juc-31F 60°C — покупал на ebay с запасом для других самоделок:
Термовключатель работает так: в обычном состоянии элемент не проводит электрический ток, цепь питания вентиляторов разомкнута. После нагрева до 60 градусов, элемент начинает проводить электрический ток и вентилятор включается. После охлаждения, как элемент остынет, цепь размыкается. Если будите покупать такие датчики, то обратите внимание — есть такие с обратной логикой — сначала включено, ток идет. После нагрева до температуры размыкания — цепь отключается. Бывают такие датчики на разную температуру крепления. Металлическая основа не прозванивается с выводами. Закрепил на радиатор, промазал предварительно термопастой.
На терминалы для акустической системы разместил цепи Зобеля и Буше — катушка, намотанная на резистор 10 Ом:
Боялся, что такое расположение катушек повлияет на характеристики усилителя (например на взаимное проникновение каналов). Но проверка в программе RMAA изменений не выявила.
Входные цепи усилителя сначала проводил экранированным проводом — три провода, каждый в отдельном экране. Но в этом случае были шумы, характерные для земляной петли. Заменил на скрученные в косичку провода. Так оказалось лучше.
Стянул провода стяжками:
Закрыл крышкой. Готовое изделие:
Итог из этого опыта переделке готового корпуса: работы по переделке сопоставимы по времени и навыками с изготовлением корпуса с нуля. По затратам — чуть меньше, чем покупка готового корпуса. Плюс — не пришлось выкидывать старое устройство, которое пылилось в чулане. У корпуса — новая жизнь. Выкинуть такое техническое устройство у меня рука бы не поднялась.
mysku.ru
БЛОГ о компьютере: моддинг: Как сделать корпус усилителя
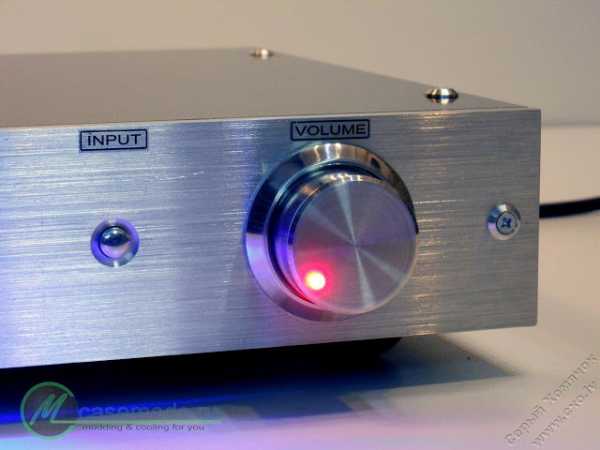
…с
некоторых пор интересуюсь «хай-фаем», конечно, если так можно сказать. В
общем: улучшаю качество домашней музыки. Ну и, соответственно ищу
всевозможные «ворклоги» и идеи по этой теме. Винтажную и самодельную
технику. И здесь хочу описать ущу один, интересный «ворк»
…
просто, очень хочется стать обладателем чего — нибудь очень дорогого и
качественного, да еще и от именитого бренда. Которых и не так уж и
много. Но, как я уже сказал слово «очень дорогого» — увы, пока это мне,
да и многим другим, не грозит.
…
узнай моя жена: сколько стоит подобный усилитель, даже если — бы я и
«нашкреб где — нибудь денег» — то это был — бы «тихий ужас». Ну это к
слову.
Что я имею в виду? «Макинтоши» и «Маранцы»:
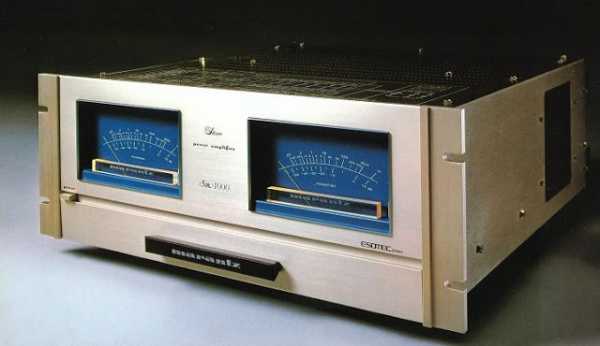
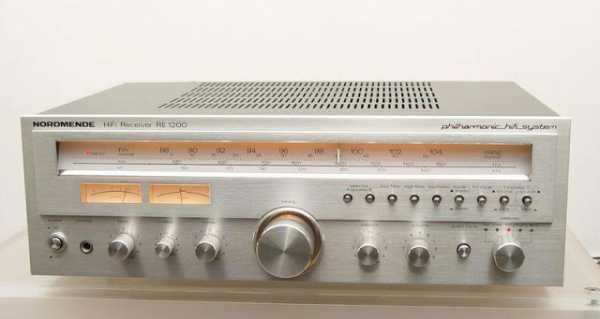
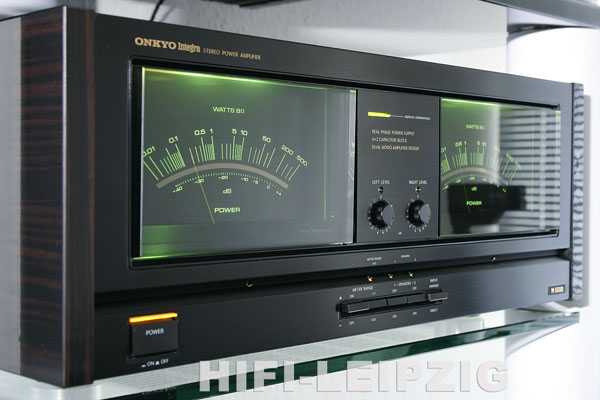

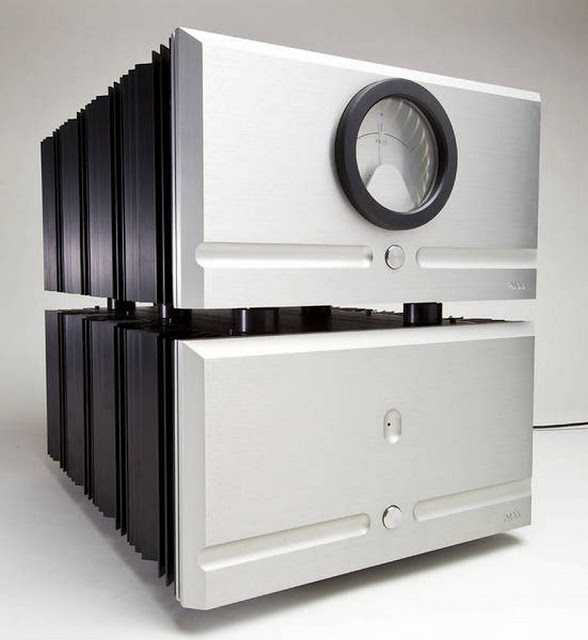
Есть и еще несколько производителей но, суть вопроса, думаю понятна.
По — этому: здесь есть несколько вариантов. Либо искать бюджетный, очень подешевевший «бэушный» компонент. Либо делать что — то похожее самому. Пусть даже старый, советский усилитель, в самодельном корпусе. Немного эффекта будет.
… ну а дальше сам пост:
Сделать усилитель не так сложно, как это кажется. Все работы можно выполнить дома на кухне, располагая минимальным набором инструмента и материала. Но тем не мене можно получить впечатляющие результаты. В этой статье я расскажу вам, как это сделать. Я так же не буду пользоваться станками и выполню все работы вручную.
Для корпуса понадобится алюминиевый угольник 15Х15 миллиметров, можно и больше, но не меньше, а то корпус не будет обладать достаточной жёсткостью. Сначала надо нарезать заготовок.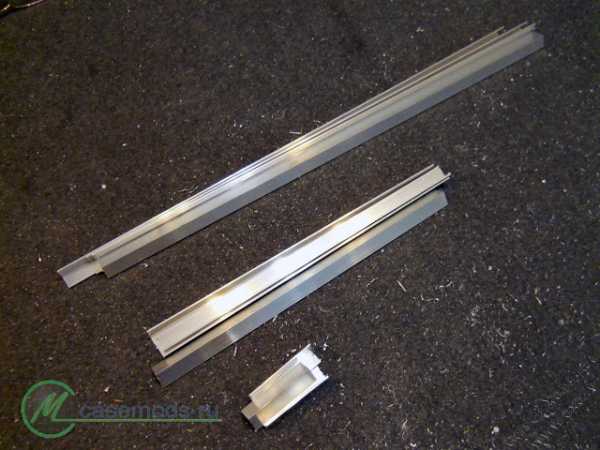
Рекомендую сначала нарисовать корпус на бумаге и просчитать все размеры, что бы потом не было мучительно больно. Когда я делаю корпуса, то исхожу из того, что все стандартные аппараты Hi-Fi класса имеют корпуса длиной 430 или 460 миллиметров, при этом их высота и глубина не лимитируется. Размер 460 миллиметров мне кажется великоватым, по этому, я принял размер 430 миллиметров.
Сам корпус планирую отделать стеклом толщиной 4 миллиметра. Из этого следует,
что каркас должен быть меньше по размерам, чем окончательный размер усилителя.
Если будет крышка из стекла 4 миллиметра и днище из алюминия толщиной 1.5
миллиметра, то высота каркаса должна быть на 5.5 миллиметра меньше планируемого
размера. А если сделать стеклянными боковины, то из общей длины надо вычесть
две толщины стекла.
Ну вот, заготовки нарезаны, можно приступать к
обработке. Начнём с вертикальных стоек каркаса. Тут тоже надо не забыть о том,
что от их высоты надо вычесть две толщины полочки применяемого угольника. В
моём случае, при общей толщине усилителя 60 миллиметров, толщине стеклянной
крышки 4 мм, днища 1.5 мм и толщине полочки угольника получилась высота стойки
51.5 миллиметров.
Все стойки я обрабатывал пакетом, это позволит
получить их одинаковую высоту.
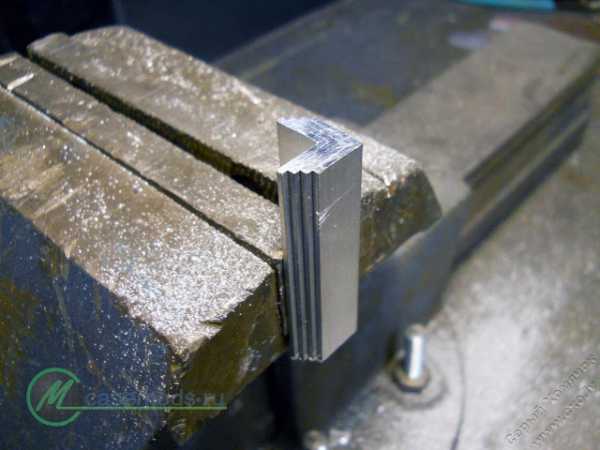
Когда стойки будут готовы, приступаем к обработке
горизонтальных элементов каркаса. Каждый конец угольника надо спилить под углом
45 градусов для удобной состыковки. Отчертить можно по школьному угольнику (я
же обещал не пользоваться профессиональным инструментом).
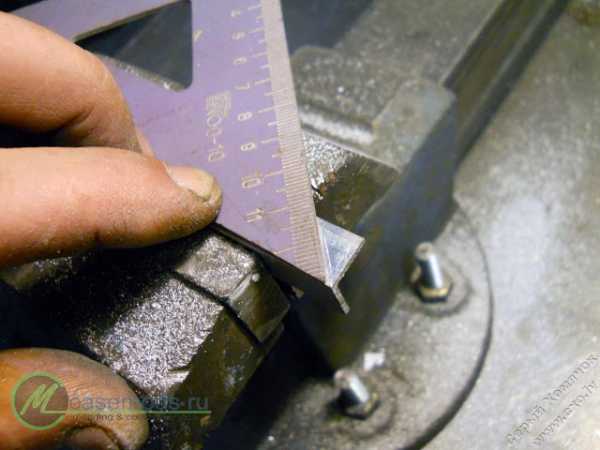
Обратите внимание на две следующие фотографии, на них видно, как надо спиливать
конец угольника.
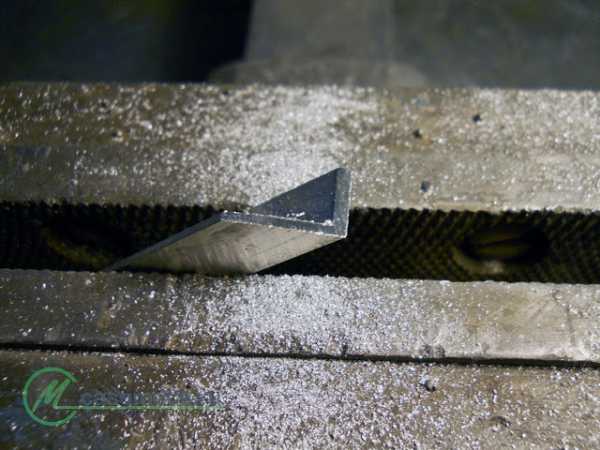
Скос должен переходить на полочку, образуя острый угол. Можно предварительно отпилить большую часть металла ножовкой, а окончательно довести напильником.
Следите за тем, чтобы все похожие детали были
одной длины. Для сборки корпуса размерами 430Х250Х60 понадобится четыре
угольника длиной 422 миллиметра, и четыре угольника длиной 250 миллиметров.
Через час у меня были все заготовки сделаны, и я приступаю к сборке каркаса.
Собирать буду на винтах М3, можно было и склепать, но
заклёпки сейчас стали дефицитом, а тяговые для этого дела не подходят – у них
будет торчать головка. Винты надо купить с потайной головкой и заточить сверло
под угол 90 градусов для высверливания углублений под головку винта.
Два угольника собираются на одной вертикальной стойке,
так, как показано на снимке.
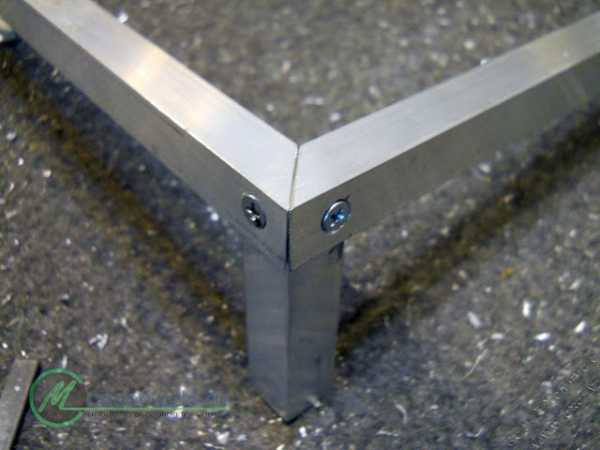
А это вид с обратной стороны.
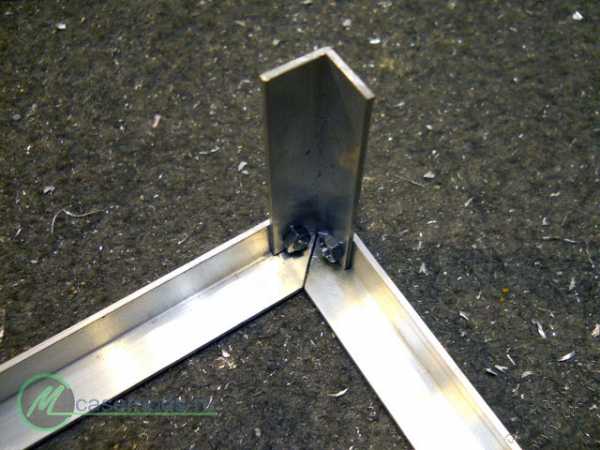
Для большей точности, можно сверлить зажав детали в
тиски.
Должно получиться нечто, похожее на аквариум.
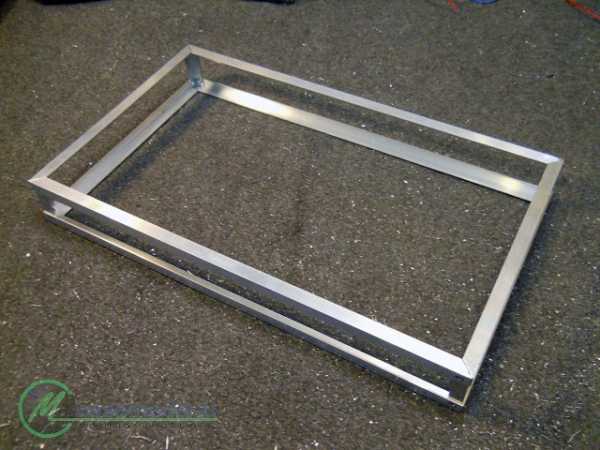
Теперь надо изготовить днище и заднюю стенку. Я их
делал из алюминиевого листа толщиной 1.5 миллиметра. Но можно применить
кровельное железо или оргстекло — хуже не будет. Только придётся пересчитать
высоту стоек. Для выпиливания заготовок я применил электролобзик, но можно их
вырезать любым доступным способом.
При вырезке не старайтесь сразу попасть в размер,
лучше сделать на миллиметр больше и окончательно подогнать по месту выступающий
край. Вот, днище готово. Его надо прикрутить к каркасу винтами с шагом не более
ста миллиметров, это исключит его прогиб.
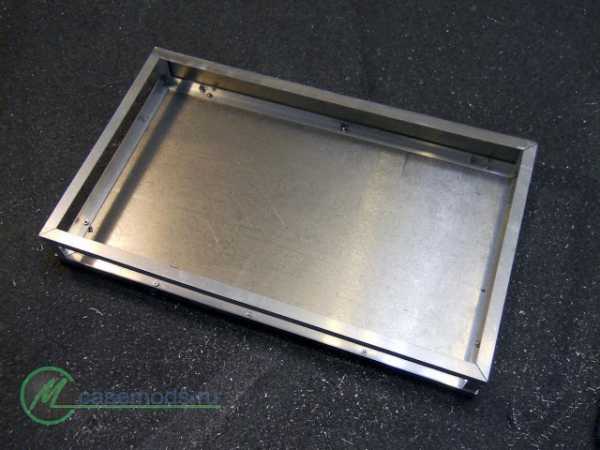
Вот теперь можно спилить в размер выступающую часть
днища.
Так же делается задняя часть корпуса. На ней будут
установлены разъём питания, входные и выходные гнёзда. Их надо приобрести
заблаговременно.
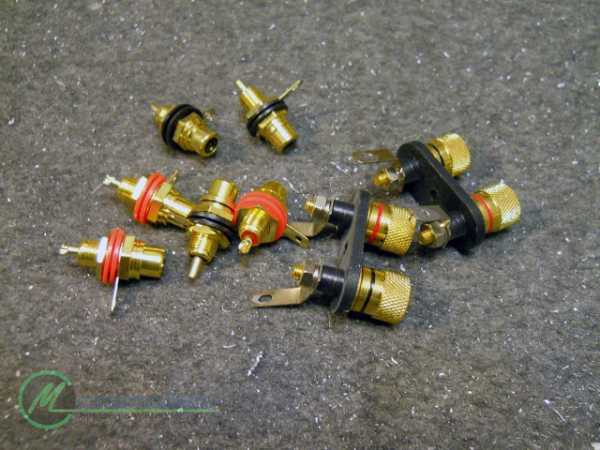
Размечаем и сверлим отверстия в задней стенке.
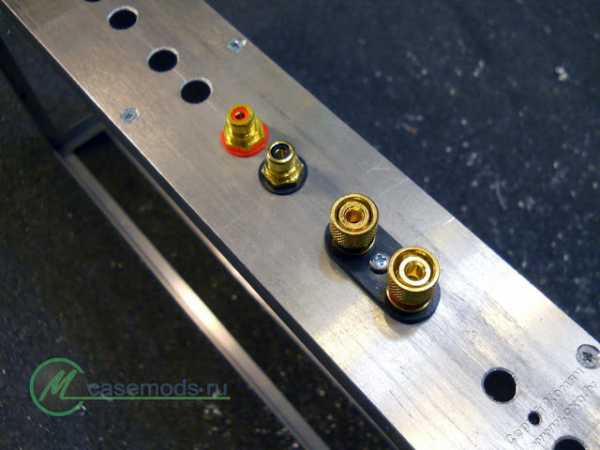
Ну, тут всё просто – отверстия круглые, а вот с
разъёмом питания придётся повозиться.
Размечаем место под будущее окно и тонким сверлом
сверлим отверстия как можно ближе друг к другу. Потом бокорезами перекусываем
перемычки…
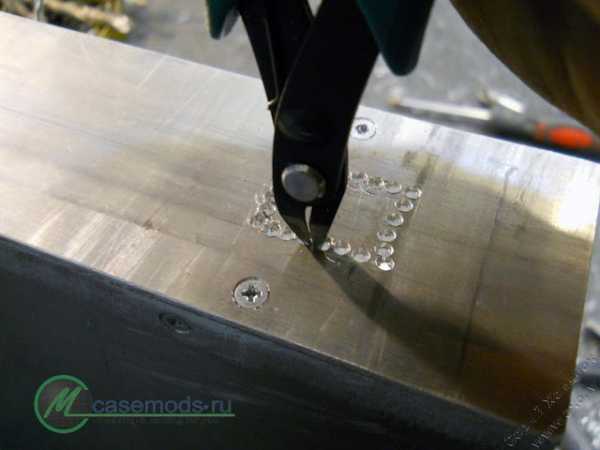
Пять минут работы напильником и окно готово!
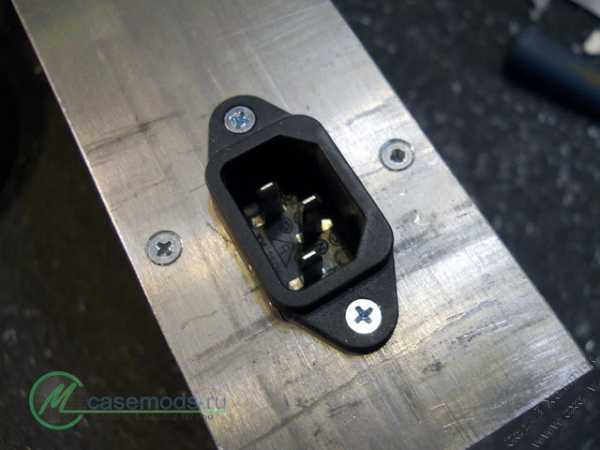
Теперь подумает о ножках нашего будущего усилителя. Их
можно применить готовые от старого компьютерного корпуса, но я нашёл ножки от
чемодана, которые сделаны из мягкого пластика. Они подошли как нельзя лучше.
Можно приступить к изготовлению передней панели. Я её
сделал из алюминиевой полосы толщиной 5 миллиметров, но это не критично, можно
и тоньше, просто толстая панель смотрится как-то красивее.
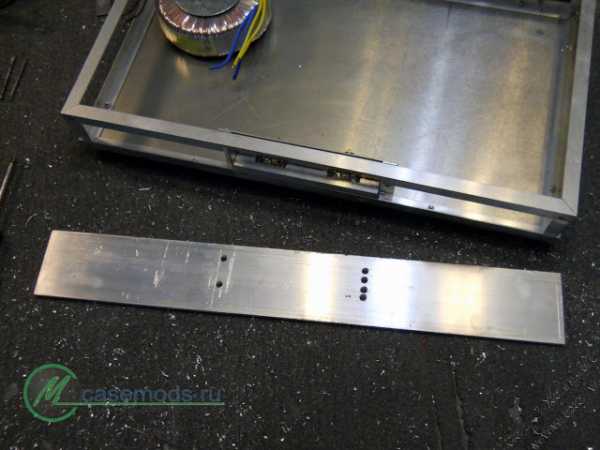
На снимке можно рассмотреть некую разметку, это то, о
чём я забыл сказать. Конкретно в этом усилителе, я захотел сделать стрелочный
индикатор уровня. Должна же быть какая-то изюминка. Но можно обойтись и без
индикаторов, кто не будет их делать – может смело пропустить всё описание про
индикаторы.
Индикаторы… Для них я приобрёл два вольтметра.
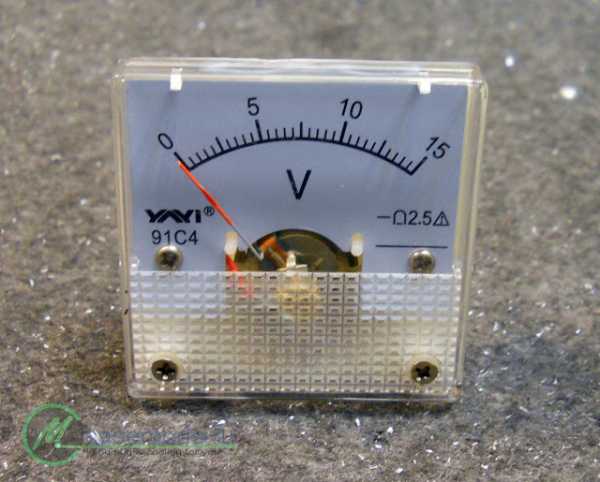
И разобрал их…
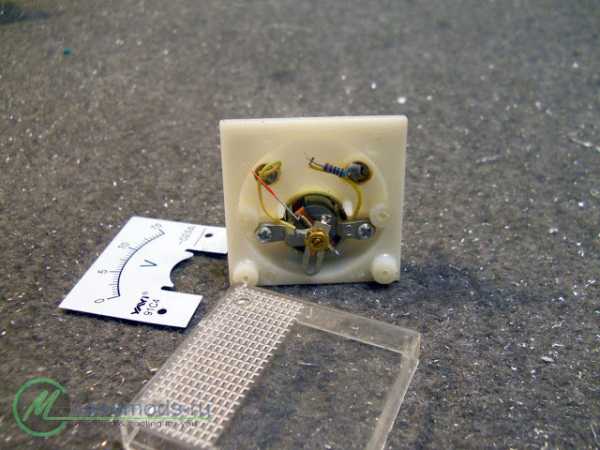
Из них нам понадобится только сам механизм. Вот с ним
надо обращаться с максимальной аккуратностью.
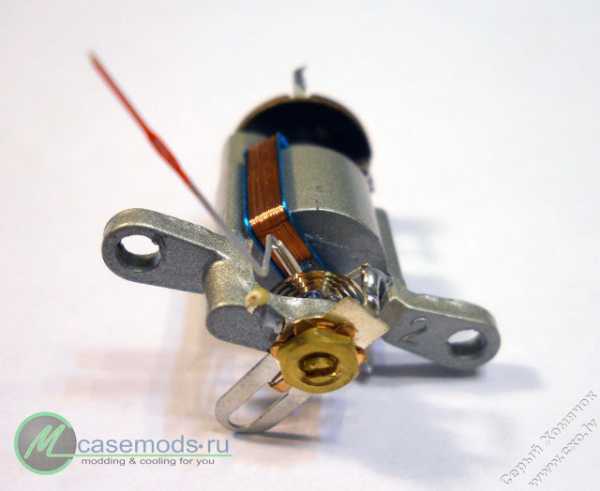
Для придания индикатору профессионального вида мы их
объединим в одном корпусе и сделаем подсветку. На алюминиевую пластину
переносим разметку с оригинального шильдика и выпиливаем надфилем.
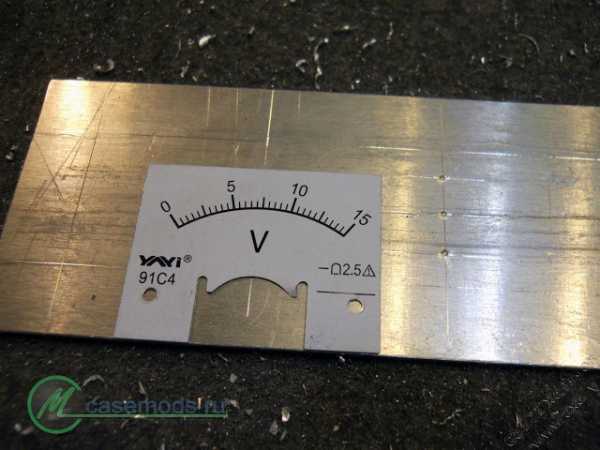
И ещё надо изготовить планку, которая прикроет
механизм от посторонних взглядов.
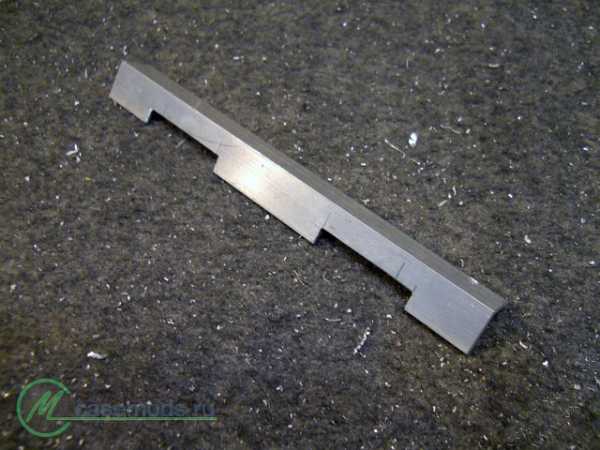
Должно получиться что-то типа того, что видно на
фотографии.
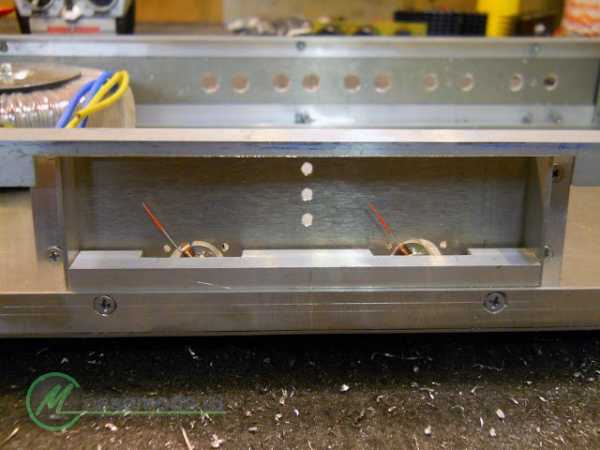
Стоит обратить внимание на боковые крышки – они нужны
для завершения конструкции. И ещё три отверстия в центре – там будут
располагаться светодиоды индикации включённого входа. Вот так это выглядит с
обратной стороны.
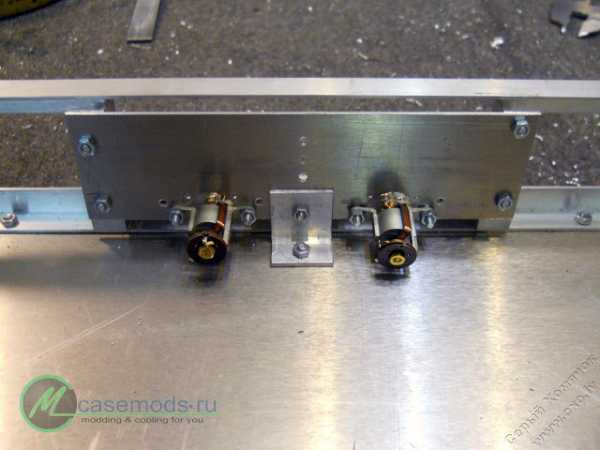
Вся конструкция держится на угольнике, который
находится посередине. Подсветка буде осуществляться полоской из синих
светодиодов. Они располагаются в верхней части корпуса, над индикатором.
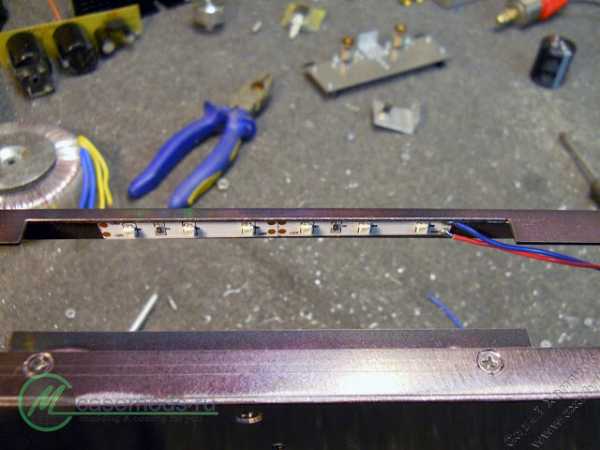
В отверстия, расположенные в центре индикатора, надо
вклеить три светодиода красного цвета свечения.
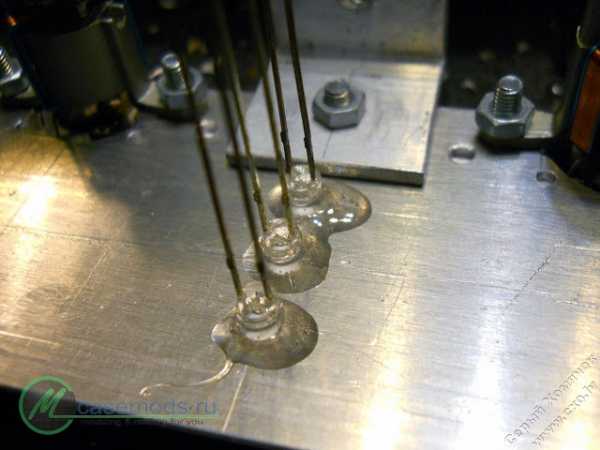
После отвердения клея, рекомендую покрыть его чёрной
краской, это позволит избежать паразитной засветки от соседних светодиодов.
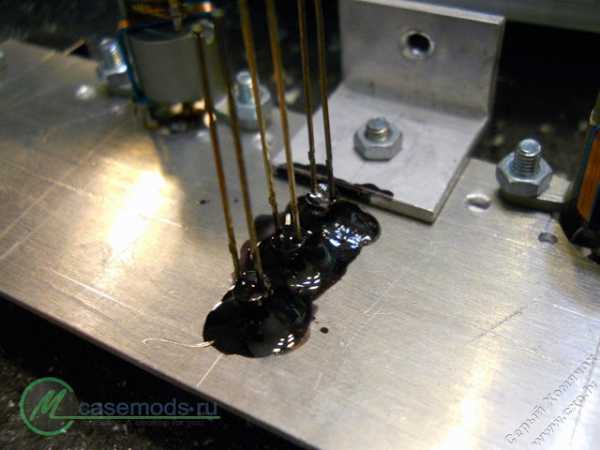
Ну и на выводы припаиваем плату с резисторами. Сами
светодиоды подключаются параллельно обмоткам реле на плате коммутации.
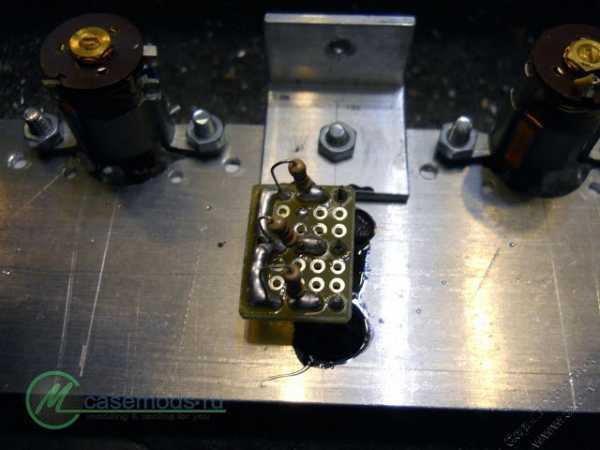
Под индикатор надо прорезать окно, воспользуемся той же технологией, что и
прорезании окна под разъём питания. Только тут надо проявить максимум
аккуратности и терпения – от этого будет зависеть внешний вид усилителя.
Тут я не удержался и профрезеровал с обратной стороны
углубление под стекло, но это не является обязательным. Можно применить тонкую
прозрачную плёнку для лазерных принтеров, эта плёнка очень тонкая и не повлияет
на размеры, что не сказать о стекле.
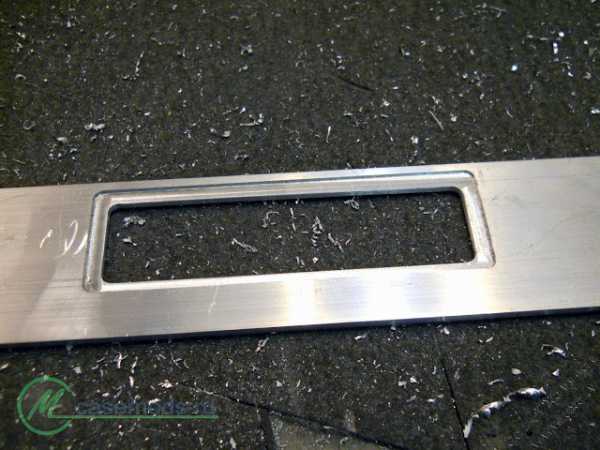
Отверстия под кнопки просверлены сверлом 8.4
миллиметра. Это потому, что у меня есть алюминиевый пруток диаметром восемь
миллиметров, из него получатся отличные кнопки.
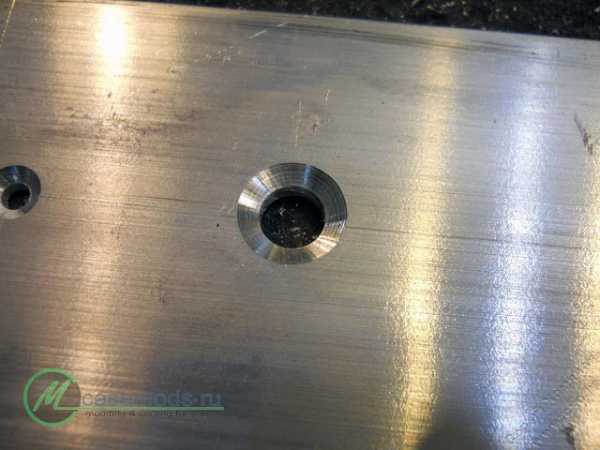
Фаску в отверстии лучше всего сделать при помощи
зенкера, сверлом трудно добиться ровной поверхности.
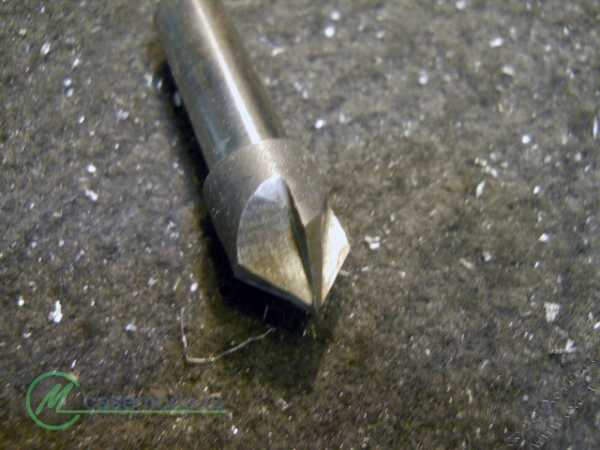
Сама кнопка отпиливается от прутка нужной длины и
шлифуется вручную при помощи ручной дрели. С обратной стороны надо просверлить
отверстие 4 миллиметра. Торец желательно отполировать.
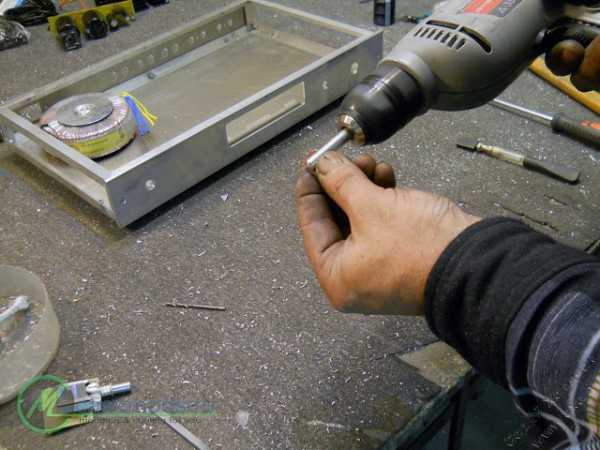
Выключатель питания крепится на двух длинных винтах, это позволит точно выставить его высоту для того, чтобы кнопка не тёрла в отверстии.
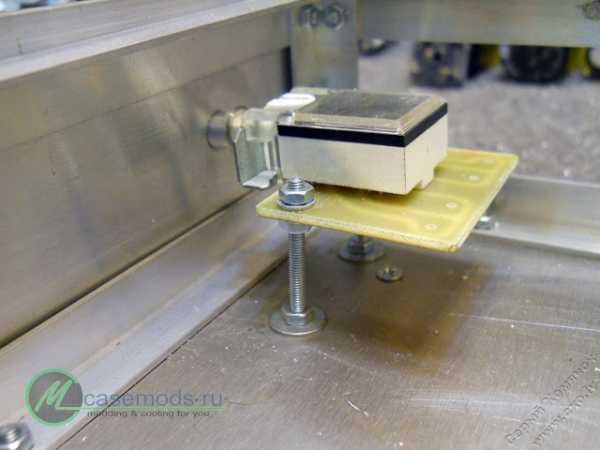
Ручку громкости можно применить готовую, это не
ухудшит внешнего вида. В продаже есть вот такие красивые ручки.
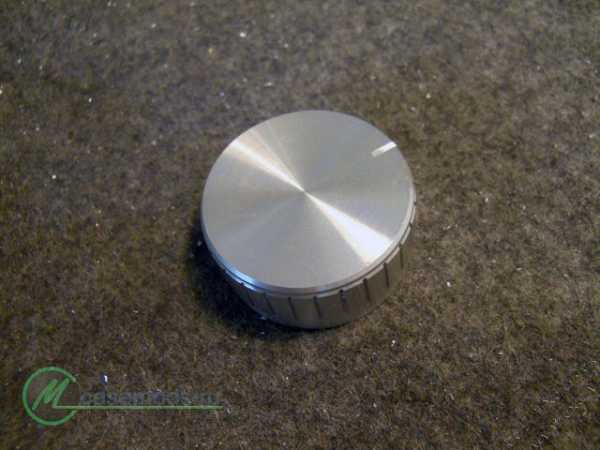
Но мне она не нравится, я применил самодельную. У кого
есть знакомый токарь – советую обратиться к нему за помощью и сделать вот такую
ручку.
И для полной завершённости надо изготовить
декоративное кольцо.
В сочетании с ручкой это примет вполне законченный
вид.
Осталась работа над отделкой корпуса. Переднюю
панель надо тщательно отшлифовать.
Для этого соберём небольшое приспособление.
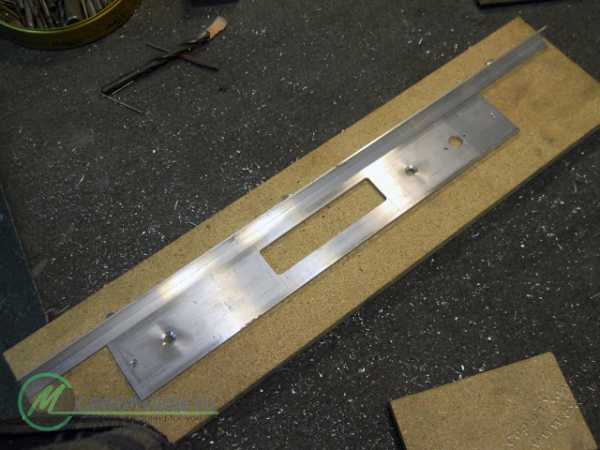
Панель закрепляется на основании из ДСП, сбоку прикручивается угольник – он
служит направляющей. Полоска наждачной бумаги со средней зернистостью
прикрепляется к отрезку того же ДСП. Наждачная бумага перемещается вдоль панели
и одновременно прижимается к направляющей. Это позволит получить параллельные
риски на панели.
При обработке панель надо обильно поливать керосином.
Его можно налить в распылитель, будет очень удобно. Панель должна быть всегда
влажной. Не трите на сухую! Могут остаться трудноустранимые дефекты.
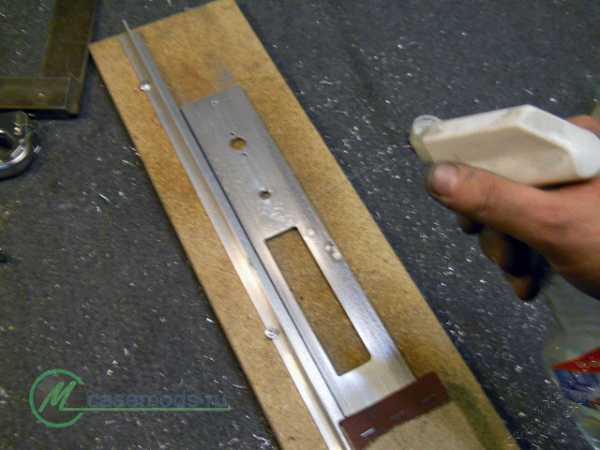
Через час можно будет полюбоваться на результаты.
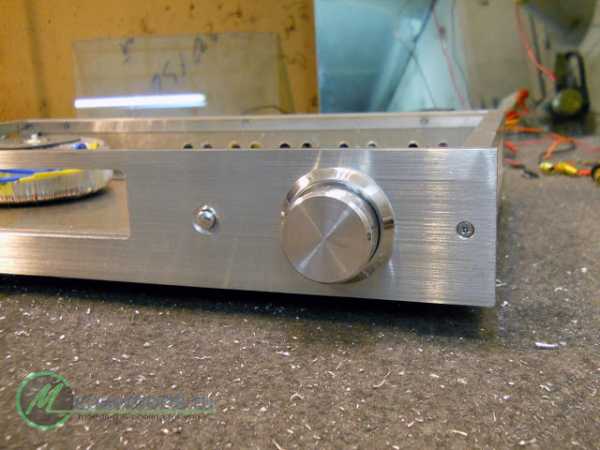
Ручку громкости можно отполировать при помощи дрели.
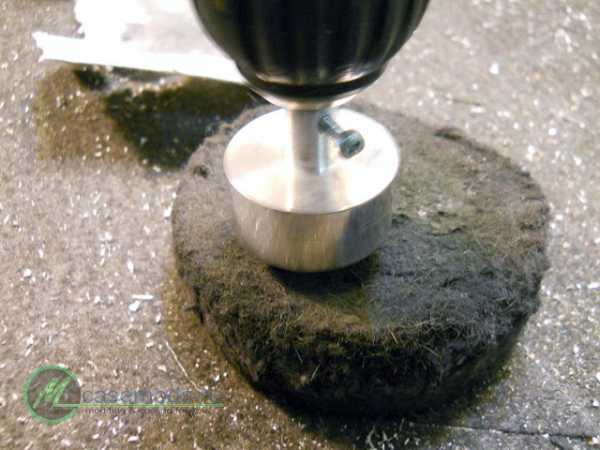
Осталось дело за малым – вырезать стёкла для отделки
корпуса. Я применил для этого зеркало серого цвета. Самое простое – заказать
всё это в зеркальной мастерской, но можно сделать самому. Отрезать стекло – не
проблема, а вот обработать кромки – это надо постараться. Обработка
производится наждачной бумагой с водой. Постепенно уменьшая номера, можно
добиться почти идеальной полировки. Но можно остановиться и на ровной матовой
поверхности.

Боковые полоски стекла приклеиваются к корпусу при помощи аквариумного силикона.
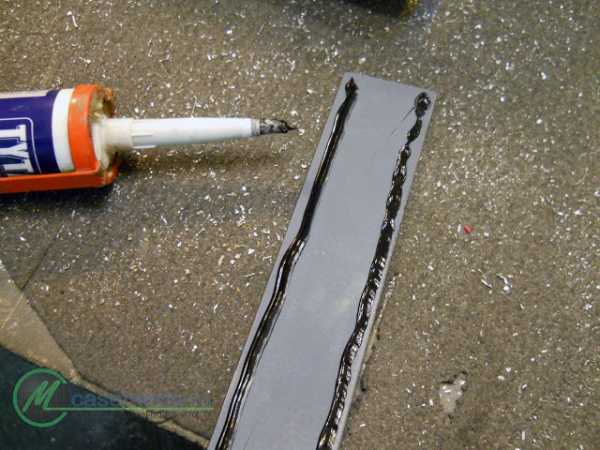
Стекло в углубление вклеивается при помощи эпоксидного клея. После отвердения,
излишки клея удаляются острым лезвием.
Собираем индикатор. Картинка для шильдика рисуется в
любом графическом редакторе и печатается на самолеящейся плёнке белого цвета.
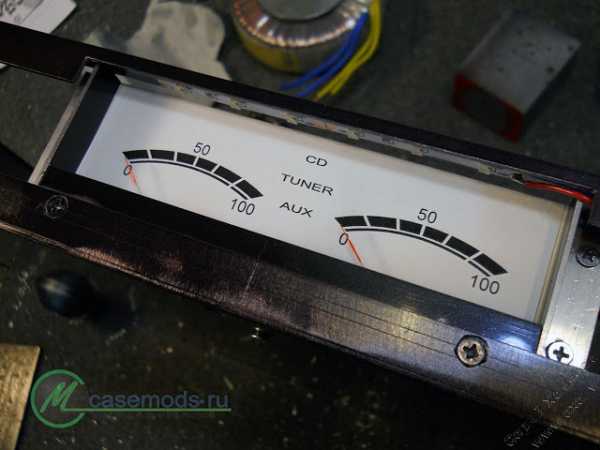
Ещё хорошо бы заказать у токаря декоративные подкладки
под винты, они придадут профессиональный вид усилителю.
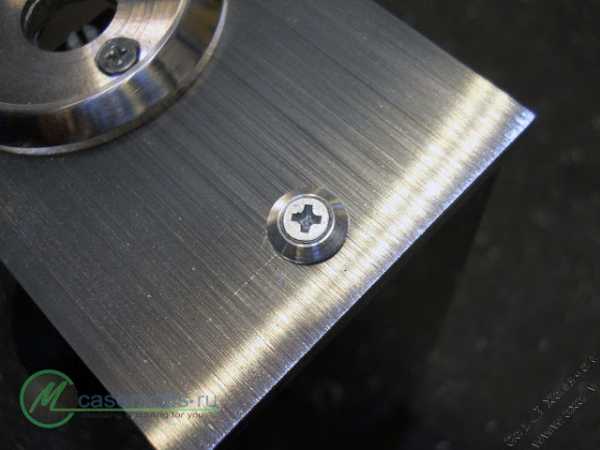
Сам корпус покрывается чёрной краской из баллончика,
но это тоже не является необходимостью – каркас почти не виден. Если крышка
корпуса сделана из стекла, кстати, хорошие результаты даёт обычное зеркало, в
ней надо просверлить отверстия. Я их делал при помощи трубчатого сверла.
Сначала до половины толщины с обратной стороны зеркала…
А потом с лицевой. Если делать наоборот, то не будет
видно, где сверлить, а насквозь сверлить не советую – в этом случае сколы
неизбежны.
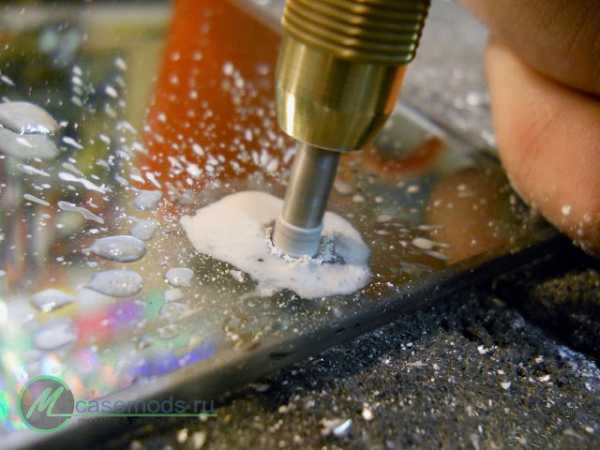
Теперь
берём светодиод красного цвета и диаметром три миллиметра. В ручке громкости
сверлится отверстие с лицевой стороны диаметром три миллиметра, а с обратной,
почти до конца, надо рассверлить его сверлом четыре миллиметра. К светодиоду
припаивается резистор, и провода изолируются трубочками. Желательно применить
провод марки МГТФ.
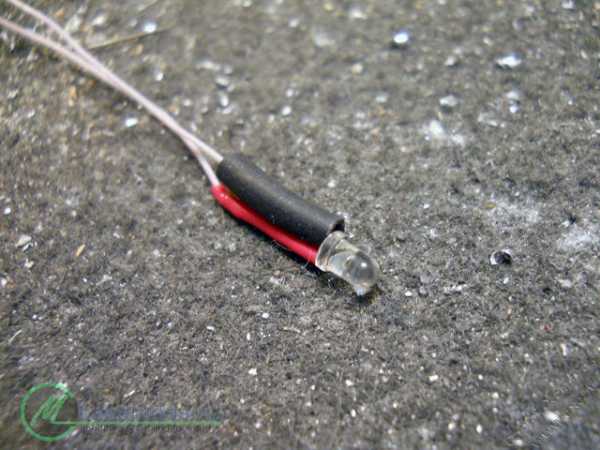
Полученная конструкция вставляется в отверстие и
закрепляется каплей клея.
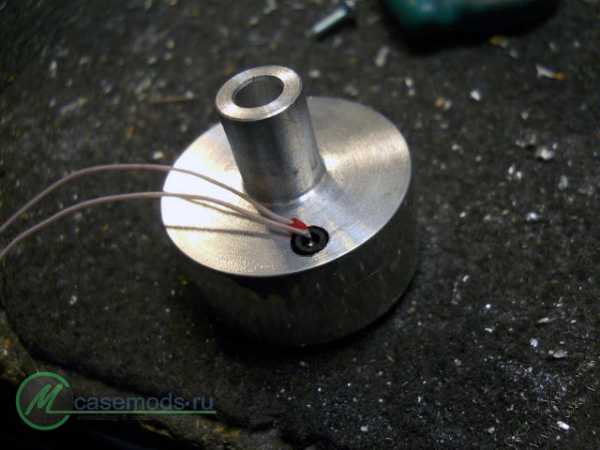
Рукоятка ставится на место, а провода пропускаются в щель между панелью и
осью.Провода от светодиода подключаются к питающему напряжению.
Вот теперь всё! Осталось закрепить верхнюю крышку. Под винтики тоже желательно подложить декоративные подкладки. Но можно применить винтики чёрного цвета.
Завершающим этапом делаем надписи на передней панели. Самый простой вариант –
напечатать их на прозрачной самоклеящейся плёнке. Я именно так и поступил.
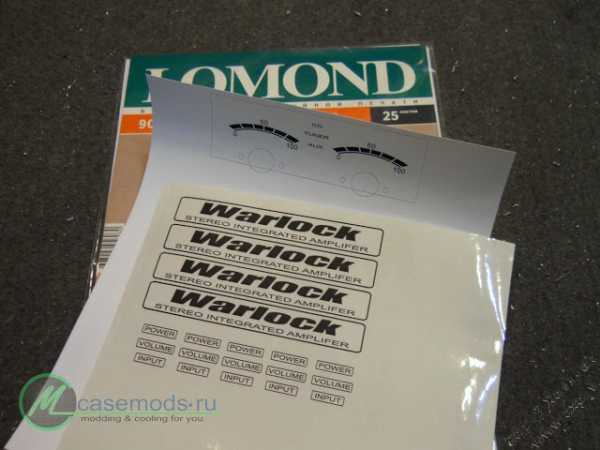
Вот, что у вас должно было получиться в итоге.
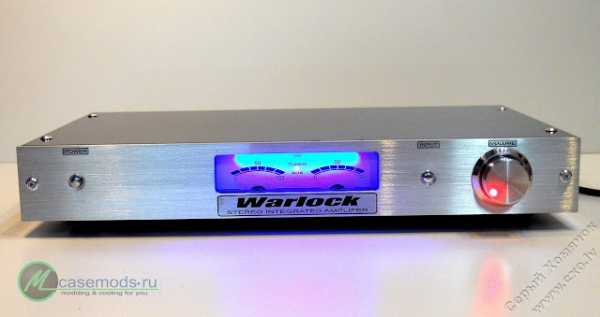
Не хвастаясь скажу, что у меня на эту работу ушло
шестнадцать часов. Так что этот усилитель вполне возможно построить за выходные
дни. Успеха!
pc-parc.blogspot.com
DIY Корпус для усилителя на базе TPA3116
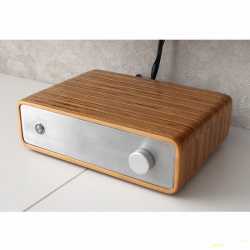
Данный обзор получился из моего расширенного комментария к обзору, сделанному мной ранее, и по совету опытных товарищей, я его оформил в отдельную публикацию.
К сожалению на этапе изготовления я не делал фото, процесс пошел очень быстро, и никакого обзора тогда и не планировалось, но в результате получилось неплохо, поэтому можно поделиться опытом не совсем сложной работы.
Для того, чтобы восполнить пробелы в наглядном представлении основных этапов, я воспроизвел процесс выполнения в SketchUp, где изначально корпус усилителя и проектировался.
Усилитель на TPA3116 был выбран в качестве временного решения, пока готовится основной усилитель, а это был длительный проект, который подходит к завершению. Плата усилителя была приобретена подобная, но без Bluetooth:
TPA3116 2*100W Bluetooth Digital Power Amplifier Board
Проект корпуса усилителя был подготовлен в SketchUp (от надписей на панели я впоследствии отказался, не совсем получалось сделать ЛУТом, и не было времени далее продолжать):
Изготовление корпуса началось с того, что был собран из подручных материалов, и имеющейся в наличии ручной циркулярной пилы (Hitachi С6SS), распиловочный стол, простой, но вполне для моих нужд подходящий.
Так как после изготовления стола осталась фанера 21мм (в реале 19мм), было решено пустить часть ее на изготовление небольшого корпуса для усилителя на TPA3116. Основными вдохновителями идеи корпуса послужили усилители от PEACHTREE AUDIO
Мне нравятся изделия из торцевого среза фанеры, поэтому было решено делать следующим образом. Из фанеры на распиловочном столе были напилены рейки высотой 15 мм (соответственно толщина среза фанеры 19 мм
Из фанерных реек, торцевым срезов вверх, были собраны три пластины, две большие для нижней и верхней части корпуса, и одна поменьше, из которой получатся две боковые стенки.
На каждую рейку нанёс клей, сжал струбцинами. Также зажал полученную пластину между двух досок снизу и сверху, чтобы рейки под струбцинами не пошли дугой.
Полученные пластины отторцевал на распиловочном столе, из пластины поменьше выпилил боковые стенки.
Далее из верхней, нижней и боковых пластин склеиваем короб, стягиваем струбцинами.
Взял корпус, взял УШМ с насадкой липучкой под шлифовальные круги (зерно 60), пошел на улицу, нарисовал радиусы на углах короба, и шлифовальным кругом снял лишний материал. Делать надо аккуратно, так как легко нырнуть рукой и снять лишнего, потом тяжело исправлять, увеличивать радиусы, а там уже толщины пластин не хватит.
Это конечно можно сделать и фрезером, но для этого фрезу покупать, я для четырех проходов как-то не выгодно.
Так как на передней части корпуса не должно быть видно стыков всех четырех деталей, то решил из фанеры толщиной 6 мм сделать переднюю окантовочную часть передней панели. Сделал чертеж передней панели, распечатал, вырезал, перенес по шаблону карандашом на фанеру, и вырезал внутреннее окно ручным фрезером (Bosch POF 1200)
Далее приклеил полученную деталь на переднюю часть короба. Опять взял УШМ с насадкой липучкой под шлифовальные круги и шлифовальным кругом снял лишний материал по периметру передней части, в соответствии с радиусами корпуса.
Переднюю панель из алюминия (толщина 4 мм) также торцуем на распиловочном столе, закругляем углы УШМ, доводим дремелем, загоняем в окантовочную часть, чтобы входила плотно, Так как окантовочная часть у нас 6 мм, то алюминиевая панель заходит с углублением 2 мм, то что нужно.
Так как алюминиевая панель была зеркальной, надо было сделать ее в стиле «шлифованный алюминий».
Пластину размещаем относительно параллельного упора в статичном положении (на двойной скотч хорошо). Берем небольшой деревянный брусок чуть больше ширины панели, оборачиваем его наждачной бумагой (зерно 80-120), крепим наждачную степлером крепко сверху бруска. Прикладываем брусок одной стороной также к параллельному упору и с одинаковым нажимом делаем движения бруском по пластине строго в одном направлении без смещений влево-вправо, иначе пойдут наклонные линии. Таких проходов надо сделать штук 20-30, смотреть чтобы цвет получался однородный и степень шлифовки одинаковой.
В алюминиевой панели сверлим отверстие для кнопки включения и для потенциометра громкости усилителя.
Заднюю панель сделал из листа вспененного ПВХ 5 мм (старый рекламный плакат, он же использован в качестве покрытия распиловочного стола). Углубление под заднюю панель выполнил прямо в корпусе, фрезером, правда немного неаккуратно, так как все на весу, не очень удобно, но и не страшно, сзади только я знаю что там косяки есть.
В листе ПВХ вырезал ножом, а где и высверлил, отверстия под терминал питания, под RCA и BANANA разъемы (достал из старого сабвуфера SVEN-620), а также разместил тумблер-переключатель входов. Насверлил вентиляционных отверстий. После заднюю панель покрасил черной краской, установил все элементы.
Тумблер-переключатель входов
Весь фанерный корпус шлифуем долго, добиваемся ровной поверхности, чтобы не чувствовались переходы между склеенными рейками если имеются. Затем всё покрывает маслом. Я использовал масло BELINKA Interier. В несколько слоев в течении двух суток. Затем полируем шерстяным кругом до блеска.
Устанавливаем внутри усилитель TPA3116, блок питания (от какого-то ноутбука, 4А, 19В), устанавливаем панели и ставим ручку потенциометра и кнопку включения. Ножки внизу усилителя резиновые, на клейкой основе, куплены в мебельной фурнитуре в Леруа Мерлен:
D Axis Volume Knob Potentiometer Knob Encoder knob 28 x 12MM
16mm Metal Annular Push Button Switch Ring LED 5-380V 12V 6V Self-lock
Корпус готов!
Надеюсь данный обзор будет полезен, у кого-то появятся новые идеи для исполнения, кто-то сможет поделиться своим опытом.
Всем спасибо за внимание!
mysku.ru
Корпус для сборки усилителя мощности
Здравствуйте. Небольшой обзор набора деталей для сборки корпуса для усилителя мощности. Хотя внешне он больше похож на лабораторный источник питанияКорпус состоит из 6 алюминиевых панелей скрепляющихся винтами. Толщина панелей 3,5 мм. Поверхность панелей сатинирована, и покрыта анодно -оксидной пленкой черного цвета. Фронтальная панель имеет толщину 7,5 мм.
В собранном состоянии корпус имеет размеры 160 х 100 х 70 мм. Внутренний размер 149 х 91 х 61 мм
К корпусу прилагаются все необходимые разъемы и гнезда, выключатель питания, рукоятка громкости, силиконовые ножки на клею.
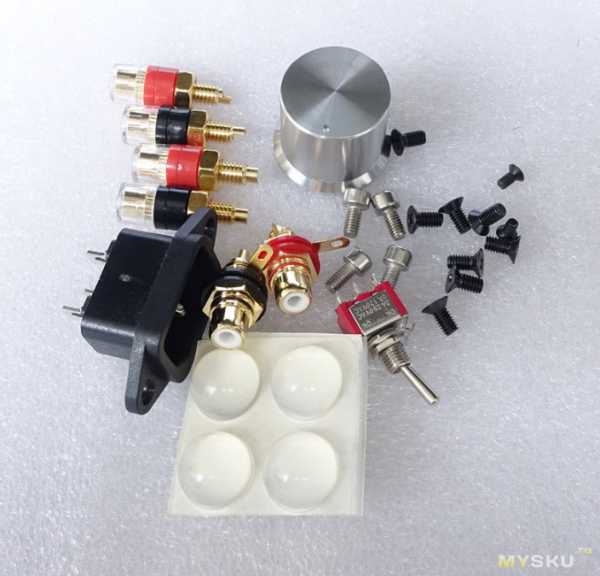
Для крепления плат предназначены пазы. Ширина пазов 2,5 мм, глубина 3,5 мм, расстояние между пазами 54 мм. Тут надо либо ухитрится купить готовый модуль именно таких размеров, либо самому все делать с нуля.
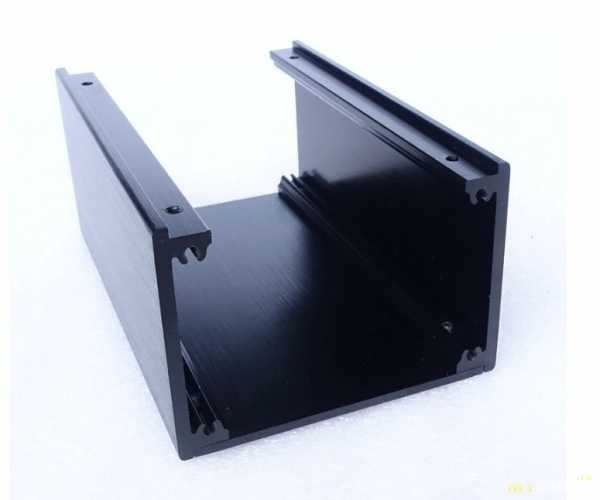
Для сборки я купил готовые модули питания и усилителя.
Модуль питания на 24 вольта 6 А
Размеры его 105 на 55 мм. В пазы он не подошел. Пришлось фиксировать термоклеем. Загнал термоклей в пазы и в отверстия на плате, сидит плата мертво. Конечно это некрасиво, но видеть это безобразие никто не будет.
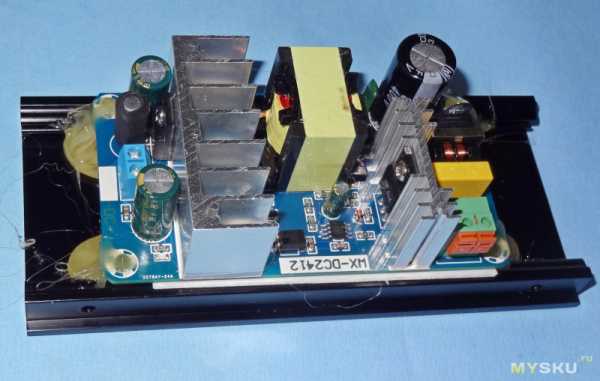
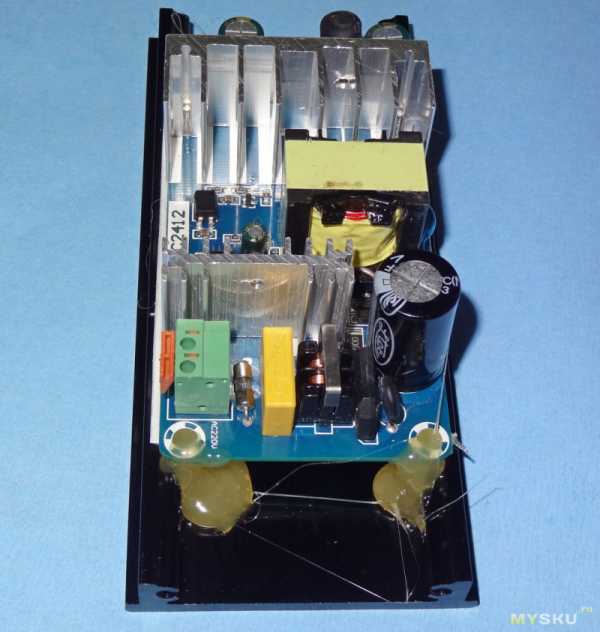
Прикрутил заднюю стенку с установленными разъемами. Паять пришлось только RCA разъемы, тумблер и розетку питания. Все остальное на винтах
Усилитель Долго искал такую плату, чтобы регулятор громкости был по центру..
Прикрутил усилитель. На всякий случай зафиксировал термоклеем.
Что удобно, конструкция позволяет собирать корпус по частям, оставляя хороший доступ к деталям.
Собираю весь корпус. Надо сказать все пригнано отлично, с точностью до сотых миллиметра… Собирать одно удовольствие.
Рукоятка громкости сделана из цельного куска алюминия, тяжелая. Фиксируется винтом. Светодиод устанавливать не стал, он есть на усилителе, надо поискать что типа толстой лески и вывести свет в отверстие.
Усилитель подключил к колонкам BBK Angel 2F
Звук порадовал. Регулировки тембров здесь нет, но желания что то подкрутить не было. Даже не предполагал, что колонки такое могут. Больше про звук распространятся не буду, это обзор корпуса, а не усилителя. Всего на усилитель было потрачено $43,72.
На этом все.
Спасибо за внимание.
mysku.ru