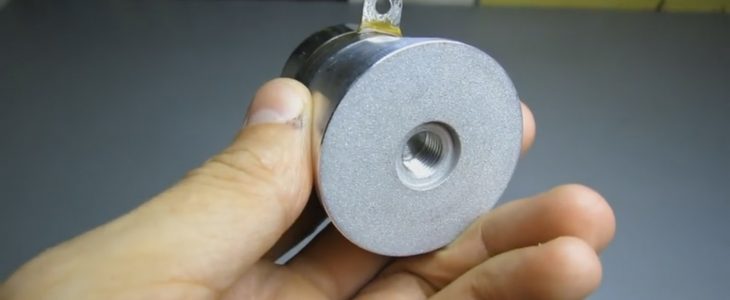
Ультразвук
Получить ультразвуковые волны довольно просто. Нужно лишь заставить вибрировать частички вещества с соответствующей частотой. Вибрацию можно осуществить следующими методами, которые и легли в основу создания ультразвуковых генераторов:
1. Механический ( акустические колебания возникают при механическом ударе по твердому телу или при его трении )
2. Пьезоэлектрический ( акустические колебания возникают при воздействии на пьезоэлектрик переменного электрического поля )
3. Магнитострикционный ( акустические колебания возникают при воздействии на ферромагнетик переменного магнитного поля )
4. Электростатический ( акустические колебания возникают при воздействии на диэлектрик переменного электрического поля )
5. Электродинамический ( акустические колебания возникают при воздействии на электропроводную среду переменного магнитного поля )
МЕХАНИЧЕСКИЕ ИЗЛУЧАТЕЛИ УЛЬТРАЗВУКА
Исторически самыми первыми были механические излучатели ультразвука. Простая стальная струна от рояля может стать источником ультразвука. Как известно, натянутая стальная струна длиной 50 см. при ударе молоточком возбуждает в воздухе звуковые волны частотой 5 кГц. Поскольку генерируемая частота обратно пропорциональна длине струны, укорачивая длину струны, можно увеличить частоту звука. Например, струна длиной 10 см. может дать ультразвук частотой 25 кГц.
При ударе молоточком по натянутой струне в окружающем пространстве возникают акустические волны
Используемые музыкантами камертоны также способны генерировать ультразвук, если уменьшить все размеры этого устройства ( предельная частота достигаемого ультразвука ~100 кГц ).
Музыкальный камертон
Однако такие простые источники ультразвука не могут дать большую акустическую интенсивность.
Более мощный ультразвук можно получить в стальном или стеклянном стержне, возбуждая в нем продольные акустические колебания посредством трения. Стержень закрепляется посередине, и один из его концов непрерывно натирается каким-либо мягким материалом типа шелковой ткани. При этом на другом конце стержня возникают акустические колебания. Среди множества генерируемых колебаний наибольшую интенсивность будут иметь те колебания, частота которых совпадает с собственной частотой упругих колебаний стержня. Независимо от материала стержня, чем меньше его длина, тем выше частота акустических колебаний.
1- Стальной стержень
2- Точка крепления стержня
3- Стальные валики, покрытые шелковой тканью
Мощным источником ультразвука ( единицы и сотни ватт ) является свисток Гальтона, работающий на частотах до 50 кГц. Принцип работы акустического свистка основан на возникновении акустических колебаний в турбулентном газовом потоке. Если в таком газовом потоке установить акустический резонатор, в нем будут усиливаться колебания, определяемые геометрией резонатора и параметрами газовой струи. Один из вариантов конструкции свистка Гальтона показан на рисунке ниже.
Газовый поток через трубку 1 подводится к кольцеобразной щели 2, через которую он попадает на острое цилиндрическое лезвие 3. При этом вокруг лезвия возникают периодические завихрения ( турбулентность ), возбуждающие в полом объеме 4 ( резонатор) акустические колебания. Резонатор настраивается подвижным поршнем 5, который приводится в движение микрометрическим винтом 6. Второй микрометрический винт 7 регулирует величину зазора между щелью 2 и лезвием 3, определяя частоту излучаемого ультразвука ( чем выше скорость газового потока и меньше ширина щели, тем выше частота акустических колебаний ). Независимая настройка резонатора и величины воздушного зазора на нужную частоту-занятие крайне утомительное. Однако при стабильном газовом потоке и четкой регулировке свисток Гальтона выдает ультразвук эталонного качества.
Разновидностью свистка Гальтона является жидкостный свисток. Принцип его работы такой же, как и газового свистка, с той разницей, что вместо газовой струи используется поток жидкости. Однако частота и мощность ультразвука в жидкостном свистке ( предельная частота ультразвука ~ 40 кГц ) ниже, чем в газовом. Это объясняется уменьшением резонансных свойств полого объема, помещенного в жидкость ( коэффициент отражения акустической волны на границе жидкость/твердое тело намного меньше, чем на границе газ/твердое тело ). Повысить мощность ультразвука, генерируемого жидкостным свистком, можно применением в качестве резонатора твердотельной пластинки. Если на пути струи жидкости поместить клиновидную пластину, в ней возникнут акустические колебания, частота которых определяется скоростью струи жидкости и расстоянием между соплом и клином пластины. Чем выше скорость потока жидкости и меньше расстояние между соплом и пластиной, тем выше частота акустических колебаний. При совпадении частоты акустических колебаний с собственной частотой колебаний пластинки возникает акустический резонанс, и амплитуда колебаний пластинки резко возрастает. Для ослабления влияния элементов держателя пластинки на амплитуду колебаний пластинка крепится в точках, в которых имеются узлы колебаний. Собственная частота колебаний клиновидной пластины определяется параметрами материала, из которого она изготовлена, но при прочих равных условиях, чем толще и короче пластина, тем выше собственная частота колебаний. На рисунке ниже стрелкой показано направление потока жидкости через сопло.
Другим механическим источником ультразвука является газоструйный акустический излучатель Гартмана.
Предельная частота ультразвука при использовании воздушной струи достигает 120 кГц. Принцип работы этого устройства основан на возникновении акустических колебаний в газовой струе, имеющей сверхзвуковую скорость истечения.
Если перед соплом 1 поместить резонатор 2, в нем будут усиливаться акустические колебания, частота которых определяется глубиной и диаметром полости резонатора.
К механическому источнику ультразвука относится и сирена. Сирена в простейшем случае представляет собой два диска, имеющих несколько отверстий, через которые продувается воздух ( бывают и жидкостные сирены, в которых вместо воздуха используется поток жидкости ). Один диск является неподвижным ( статор ), а другой ( ротор ) вращается параллельно статорному диску. Если оба диска имеют одинаковые отверстия, то за счет периодического прерывания потока воздуха возникают акустические колебания определенной частоты, зависящей от числа отверстий в дисках и частоты вращения ротора. Чем больше отверстий в дисках и выше число оборотов ротора, тем выше частота излучаемого ультразвука.
Предельная частота ультразвука сирены достигает 50 кГц, хотя в оригинальных конструкциях частота ультразвука составляет несколько сотен килогерц. Сирена способна выдавать акустическую мощность в несколько киловатт. Ультразвуковое поле сирены может быть настолько большим, что помещенный в него клочок ваты практически мгновенно вспыхивает и сгорает.
Практическое использование описанных выше механических излучателей ультразвука сильно ограничивается тем обстоятельством, что ультразвук генерируется в газовой струе, тогда как часто требуется введение ультразвука в жидкость или твердое тело.
ЭЛЕКТРОСТАТИЧЕСКИЙ ИЗЛУЧАТЕЛЬ УЛЬТРАЗВУКА
Принцип работы электростатического акустического генератора основан на взаимодействии электрически заряженных частиц. Как известно, однополярные заряды отталкиваются друг от друга, а разнополярные притягиваются. Если зарядить две параллельные металлические пластины разными зарядами, то пластины будут взаимно притягиваться. Если же подать на пластины переменное напряжение, пластины начнут совершать механические колебания, частота которых будет определяться частотой переменного напряжения. Как правило, в электростатическом излучателе одна пластина неподвижна, а другая представляет собой тонкую ( десятки микрон ) металлизированную пленку, которая и совершает колебания, возбуждая продольную акустическую волну.
Электростатический излучатель способен генерировать ультразвук довольно большой частоты, исчисляемой десятками мегагерц, однако интенсивность получаемого ультразвука относительно мала.
ЭЛЕКТРОДИНАМИЧЕСКИЙ ИЗЛУЧАТЕЛЬ УЛЬТРАЗВУКА
На любой проводник с током, находящийся в магнитном поле, действует сила Лоренца. Это явление используется в электродинамическом акустическом генераторе. На рисунке показан простой электродинамик, способный излучать ультразвук.
Если в проводе катушки протекает переменный ток, его магнитное поле наводит вихревые токи в электропроводящем стержне, заставляя его совершать механические колебания. Стержень соединен с мембраной, которая и создает в окружающей среде продольную акустическую волну, частота которой зависит от частоты переменного тока в катушке. Электродинамики применяют для генерации низкочастотного ультразвука, частота которого не превышает 100 кГц. Электродинамический принцип получения ультразвука используют, главным образом, в микроэлектронике при создании так называемых электромагнитных акустических преобразователей. Работа таких преобразователей основана на возникновении акустических колебаний в твердом теле, на которое действует внешнее магнитное поле. При прохождении через твердое тело электрического тока на него действует сила Лоренца со стороны внешнего магнитного поля, и при переменном токе в твердом теле возникают акустические колебания, частота которых зависит от частоты переменного тока. В миниатюрных преобразователях в качестве твердого тела применяют металлизированный диэлектрик (стекло или керамика ).
МАГНИТОСТРИКЦИОННЫЙ ИЗЛУЧАТЕЛЬ УЛЬТРАЗВУКА
Эффект магнитострикции уже давно используется для генерации ультразвуковых колебаний. В чем суть ? Если поместить ферромагнитный стержень в переменное магнитное поле, геометрические размеры стержня будут изменяться, т.е. в окружающей стержень среде возникнут акустические волны.
При совпадении частоты переменного магнитного поля с собственной частотой упругих колебаний стержня возникнет акустический резонанс, и амплитуда колебаний стержня будет максимальной.
Амплитуда колебаний стержня-вибратора зависит не только от физических свойств конкретного ферромагнетика, но и от упругости твердого тела, из которого изготовлен стержень. Вобщем-то, амплитуда акустических колебаний незначительна и исчисляется микронами, но и этого достаточно для создания высокоэффективных ультразвуковых технологических установок.
В качестве материала для магнитострикционного преобразователя (вибратора) среди металлов-ферромагнетиков никель обладает самыми лучшими магнитострикционными свойствами, однако были найдены и другие материалы на основе интерметаллических соединений:
Альфер -сплав Fe и Al (13% )
Пермаллой -сплав Fe и Ni (40%)
Альсифер -сплав Fe и Al (4%), Si (2%)
Пермендюр -сплав Fe и Co (49%), V (2%)
Инвар -сплав Fe (64%) и Ni (36%)
Цекас -сплав Fe (26,9%), Ni (59,9%), Cr (11,2%), Mn (2%)
Альтернативой перечисленным выше материалам является ферритовая керамика, химический состав которой определяется общей формулой MO-Fe2O3, где М может быть таким металлом как Ni, Co, Fe, Mn, Mg, Cu. Преимущество ферритового вибратора в том, что у него потери на вихревые токи значительно ниже, чем у металлического вибратора, что позволяет использовать монолитные вибраторы на высоких частотах ультразвука. Если металлический вибратор при продолжительной работе требует водяного охлаждения, то ферритовый вибратор способен генерировать ультразвук при температуре до 500 °. Однако феррит не выдерживает мощных ультразвуковых вибраций и его применение ограничено.
На рисунке ниже показана конструкция самодельного магнитострикционного вибратора на основе ферритового стержня.
Вибратор металлического магнитострикционного излучателя представляет собой стянутый в единый пакет набор из пластин ( толщина пластины не более 0,3 мм ). Для возбуждения ультразвуковых колебаний вокруг пластин вибратора наматывается несколько витков провода, через который пропускается переменный ток ультразвуковой частоты.
Магнитострикционный преобразователь, набранный из отдельных пластин ( справа на рисунке форма отдельной пластины).
Для получения максимальной амплитуды акустических колебаний длина пластины соответствует резонансной частоте. Если требуется облучать ультразвуком большие поверхности, используют более сложные профили пластин. На рисунке ниже показан магнитострикционный преобразователь для ванн ультразвуковой очистки.
В некоторых ультразвуковых приборах требуется направленное ультразвуковое излучение. В этом случае применяют преобразователь, набранный из пластин круглого профиля.
Магнитострикционный преобразователь, в котором используются ультразвуковые колебания внешнего кольца пакета пластин.
Магнитострикционный преобразователь, в котором используются ультразвуковые колебания внутреннего кольца пакета пластин.
Как правило, в магнитострикционном излучателе используется подмагничивание вибратора, что позволяет добиться большей амплитуды колебаний вибратора. При этом частота колебаний вибратора совпадает с частотой переменного магнитного поля ( без подмагничивания частота вибратора вдвое больше частоты магнитного поля, но амплитуда вибраций будет незначительной ). В ферритовых излучателях для подмагничивания обычно применяют постоянные магниты, а в металлических излучателях используют подмагничивание постоянным током, проходящим через обмотку возбуждения вибратора или дополнительную обмотку подмагничивания. Принципиального значения источник подмагничивания не имеет. В любом случае, для конкретного вибратора существует оптимальная величина магнитного поля, при которой достигается максимальная амплитуда ультразвуковых колебаний.
На рисунке ниже показана схема подключения магнитострикционного преобразователя (вибратора) с подмагничиванием электрическим током.
В этой схеме разделительный конденсатор С препятствует закорачиванию блока питания через выходные цепи ультразвукового генератора, а дроссель препятствует проникновению высокочастотных колебаний в блок питания.
Применение в магнитострикционных преобразователях вибратора, набранного из отдельных металлических пластин, обусловлено необходимостью уменьшения нагрева металла в электромагнитном поле катушки возбуждения. При использовании монолитного вибратора возрастают потери энергии на вихревые токи, что приводит к нагреву ферромагнетика вибратора особенно на высоких частотах ультразвука. Как известно, при нагревании ферромагнетик теряет свои магнитострикционные свойства и при определенной температуре ( точка Кюри) превращается в парамагнетик, что приводит к полному прекращению ультразвуковых колебаний вибратора.
Предельная частота ультразвуковых колебаний магнитострикционного излучателя определяется его геометрическими размерами ( чем меньше длина вибратора, тем выше частота ультразвука ) и не превышает 200 кГц. Однако при некоторой потери мощности можно получить ультразвук гораздо большей частоты, возбуждая вибратор на частотах, кратных гармоникам собственной частоты упругих колебаний вибратора. Так, например, применяя в качестве вибратора тонкую ферритовую пластинку, можно получить ультразвук частотой порядка 10 МГц.
ПЬЕЗОЭЛЕКТРИЧЕСКИЕ ИЗЛУЧАТЕЛИ УЛЬТРАЗВУКА
Принцип работы пьезоэлектрического излучателя ультразвука основан на использовании обратного пьезоэффекта, т.е. возникновении механических деформаций в некоторых кристаллах при воздействии на определенные грани кристалла внешнего электрического поля. Пьезоэлектрический эффект позволяет генерировать самый широкий спектр ультразвуковых частот. Только пьезоэлектрические излучатели способны создавать высокочастотные акустические колебания с частотой порядка 100 МГц.
Главным элементом пьезоизлучателя является твердотельная пластина ( иногда полимерная пленка ), изготовленная из пьезоэлектрического материала ( кварц, турмалин, кристалл сегнетовой соли, титанат бария, цирконат-титанат свинца ). Пластина помещается между двумя электродами, на которые подается переменное электрическое напряжение ультразвуковой частоты. Если пластина изготовлена из кристаллического пьезоэлектрика, то направление ультразвукового излучения будет зависеть от того, как ориентированно внешнее электрическое поле относительно кристаллографических осей пластины. Возможны как продольные, так и поперечные колебания пластины.
В результате пьезоэффекта в окружающей пластину среде возбуждаются акустические колебания, частота которых определяется частотой источника переменного напряжения. Амплитуда таких колебаний пропорциональна величине приложенного к электродам напряжения и ограничена диэлектрической прочностью материала пластины. Кроме того, акустические колебания будут максимальными, если частота переменного напряжения совпадает с собственной частотой упругих колебаний пластины.
В настоящее время все технологические, медицинские и бытовые ультразвуковые установки с пьезокерамическим преобразователем используют не дорогие пьезокристаллы, а дешевую пьезокерамику на основе титаната бария или цирконат-титаната свинца. В зависимости от направления поляризации пьезокерамического вибратора в нем могут возникать как продольные, так и поперечные колебания. В таблице ниже показаны самые распространенные виды пьезокерамических излучателей.
Пьезокерамические вибраторы могут иметь различную форму и размеры
На рисунке ниже представлена одна из возможных конструкций пьезокерамического преобразователя.
Акустические свойства и площадь поперечного сечения металлических частей преобразователя должны соответствовать таковым для пьезокерамики. Обе металлические части могут быть изготовлены из одинакового или комбинированного материала. Обычно используют сталь, алюминий, титан, магний, бронзу, латунь и медь. Часто только одна из металлических частей используется для выхода максимальной мощности, и преобразователь изготавливается как полуволновой вибратор с резонансной частотой от 20 кГц до 40 кГц. Для увеличения предела прочности пьезокерамического элемента, а также улучшения акустического контакта металлические части преобразователя стягиваются болтом, создавая предварительное механическое напряжение на пьезокерамике.
ultrasound.ucoz.ru
Пьезоэлектрический излучатель — Википедия
Материал из Википедии — свободной энциклопедии
Текущая версия страницы пока не проверялась опытными участниками и может значительно отличаться от версии, проверенной 28 февраля 2017; проверки требуют 2 правки. Текущая версия страницы пока не проверялась опытными участниками и может значительно отличаться от версии, проверенной 28 февраля 2017; проверки требуют 2 правки. Биморфный пьезоэлемент Звук пьезоизлучателяПьезоэлектри́ческий излуча́тель, пьезоизлуча́тель — электроакустическое устройство, способное воспроизводить звук, либо излучать ультразвук, благодаря обратному пьезоэлектрическому эффекту.
Пьезоэлектрический излучатель состоит из металлической пластины, на которую нанесён слой пьезоэлектрика, имеющий на внешней стороне токопроводящее напыление. Пластина и напыление являются двумя контактами. Для увеличения громкости звука к металлической пластине может крепиться небольшой рупор в виде металлического или пластикового купола с отверстием[1]. В качестве рупора также может использоваться углубление в корпусе устройства, в котором используется пьезоизлучатель.
Пьезоэлектрические излучающие элементы могут иметь сферическую или цилиндрическую форму поверхности[2].
- Номинальное напряжение звукового сигнала [V]
- Допустимое напряжение звукового сигнала [V]
- Рабочий ток (при напряжении[V], частоте [KHz]) [mA]
- Ёмкость (на частоте [Hz]) [pF]
- Резонансная частота [Hz]
- Звуковое давление (на расстоянии [cm]) [dB]
- Диапазон рабочих температур [°C]
- Габаритные размеры [mm]
- Масса [g]
Пьезоизлучатели отечественного производства[править | править код]
Отечественные пьезоизлучатели имеют обозначения, состоящие из букв «ЗП» (звукоизлучатель пьезоэлектрический) и номера серии. Наиболее распространённые в отечественной бытовой технике излучатели — ЗП-1 и ЗП-3.
Звукоизлучатели типа ЗП приводятся в действие подачей переменного напряжения определённой частоты и амплитуды, обычно, 3…10 В. Частота, при которой звуковое давление максимально, может достигать 75 дБ на расстоянии 1 метр от излучателя. Резонансная частота для большинства пьезоизлучателей составляет 1…4 кГц. Этим обусловлен их характерный, узнаваемый звук, напоминающий «пип».
Пьезоизлучатели широко используются в различных электронных устройствах — часах-будильниках, телефонных аппаратах, электронных игрушках, бытовой технике. Часто используются в качестве излучателей ультразвуковых колебаний в устройствах отпугивания грызунов и насекомых, увлажнителях воздуха, ультразвуковых «стиральных машинах» (см. ультразвуковая очистка).
Пьезоизлучатель также может использоваться в качестве пьезоэлектрического микрофона или датчика.
ru.wikipedia.org
Ультразвуковые преобразователи. Ультразвуковые датчики.
Пьезоэлектрические преобразователи нашли широкое применение в различных областях, начиная от зажигалок и заканчивая медицинскими исследованиями. Наиболее часто встречающаяся конструкция преобразователя представлена на рисунке 1. Такой тип передатчика обычно применяется для излучения ультразвуковых волн в жидкую или твердую среду, а также для измерения расхода газа. Активным элементом преобразователя является пьезоэлемент (пьезокерамический диск), который как показано на рисунке 1 находится между согласующим слоем и демпфером. Два электрода на верхней и нижней поверхности диска соединены с генератором сигналов. Согласно пьезоэлектрическому эффекту, пьезоэлектрический диск будет колебаться, когда синусоидальное переменное напряжение прикладывается к электродам пьезоэлектрического диска. Колебание диска связано с частотой переменного синусоидального напряжения и размерами диска [1].
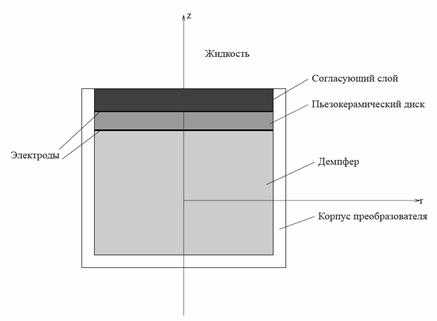
Рисунок 1 – Конструкция пьезоэлектрического преобразователя
Обычно пьезоэлектрический материал с высоким коэффициентом электромеханической связи имеет большое волновое сопротивление по сравнению с водой и воздухом. Поэтому, полоса пропускания частотной характеристики диска ниже. Неподходящее волновое сопротивление можно преодолеть, используя передний (согласующий) и задний (демпфер) слои между пьезоэлектрическим диском и жидкой средой, как показано на рисунке 1.
Задний слой обычно имеет высокий коэффициент затухания, высокую плотность материала, которая требуется для того чтобы контролировать колебания преобразователя путем поглощения энергии излучаемой пьезоэлементом назад.
Когда акустическое сопротивление задней части совпадает с волновым сопротивлением активного элемента (пьезокерамики), результатом будет сильно демпфированный преобразователь, который демонстрирует хорошую область разрешения, что связано с широкой полосой частот обеспечиваемой передатчиком, но при этом он может иметь меньшую амплитуду сигнала.
Если акустический импеданс пьезоэлемента и задней части не совпадает, больше звуковой энергии будет отражаться вперед в исследуемое вещество. Конечным результатом является преобразователь, который имеет меньшее разрешение, вследствие более длиной продолжительности осциллограммы, но может иметь более высокую амплитуду сигнала и лучшую чувствительность.
Основная цель согласующего слоя преобразователя заключается в том, чтобы защитить пьезоэлемент от исследуемого вещества. Согласующий слой должен быть прочным и коррозионностойким к исследуемой жидкости. Дополнительно передний слой должен связывать высокое акустическое сопротивление пьезокерамики с низким акустическим сопротивлением жидкости. Толщина согласующего слоя выбирается равной четверти длины волны. Это основано на идеи суперпозиции волн находящихся в одной фазе, что увеличивает амплитуду сигнала в два раза.
Существует много подходов для того чтобы сделать оптимальный выбор толщины и волнового сопротивления заднего и переднего слоя, некоторые из которых отражены в следующих работах [2, 3, 4, 5, 6, 7]. Пьезоэлектрический преобразователь может быть использован как в качестве излучателя, так и в качестве приемника. В режиме передатчика ультразвуковая волна создается пьезокерамикой, к которой прикладывается напряжение. В режиме приемника, пьезокерамика преобразует приходящую акустическую волну в электрический сигнал. В некоторых случаях преобразователь используется одновременно как приемник и как передатчик. Преобразователь может работать в режиме возбуждения пьезокерамики непрерывной синусоидально волной, или в импульсном режиме.
В низкочастотном ультразвуковом диапазоне используют преобразователи следующей конструкции (рисунок 2).
Рисунок 2 – Конструкция ультразвукового преобразователя
Активный элемент ультразвукового преобразователя состоит из двух пьезокерамических пакетов, между которыми находится металлический цилиндр. Все элементы прибора фиксируются и сжимаются под определенным усилием с помощью стального болта, который вызывает начальную поляризацию пьезокерамических пакетов. Амплитуда колебаний такого преобразователя зависит от количества пьезокерамик, от характеристик используемых материалов. Максимальные колебания кончика излучателя такого преобразователя могут достигать десяти микрон на резонансной частоте. Пьезокерамический преобразователь стандартной конструкции (с цилиндрическим излучателем) на самом деле совершает колебания маленькой амплитуды. Общей практикой для усиления механических колебаний является использование конусной формы излучателя и излучателей с экспоненциальной формой. В области высоких ультразвуковых мощностей длину излучателя делают равной половине волны резонансных колебаний [8].
В качестве примера рассмотрим конструкцию ультразвукового бура, разработанного для марсоходов Спирит и Оппортьюнити, предназначенных для программы NASA исследования планет солнечной системы (рисунок 3). Он состоит из трех главных компонентов: ультразвукового вибратора, свободной массы и буровой штанги (рисунок 3).
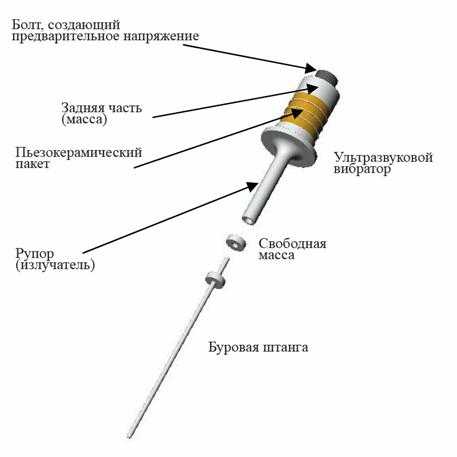
Рисунок 3 – Ультразвуковой бур
Ультразвуковой вибратор состоит из пакета круглых пьезокерамик, ультразвукового рупора, металлической задней части и болта, создающего первоначальное напряжение, чтобы плотно соединить все эти части и обеспечить предварительное напряжение на пьезокерамический пакет. Пьезокерамический материал должен быть под первоначальной нагрузкой, чтобы не выйти из строя во время деформации. Пьезоэлектрический пакет работает на резонансной частоте ультразвукового вибратора. Через усиливающий ультразвуковой рупор, смещение колебаний достигает 10 микрон на кончике рупора (излучателя). Свободная масса соединена с кончиком ультразвукового рупора бура. В течение операции взятия пробы, свободная масса балансирует и двигается назад и вперед между ультразвуковым рупором и буровой штангой. Благодаря тому, что скорость колебаний свободной массы меньше чем скорость колебаний кончика рупора, свободная масса обычно контактирует с кончиком рупора в подходящей фазе колебаний кончика рупора. В момент, когда свободная масса достигает рупора, она ускоряется и двигается назад к буровой штанге. Свободная масса передает ударные импульсы от ультразвукового преобразователя к буровой штанге с частотой от 10 Гц до 1000 Гц. Ударные волны возникают из-за удара свободной массы по буровой штанге и распространяются к камню/грунту. Под ударом хрупкая среда (камень, лед и т.д.) разрушается, когда его предельная деформация превышается [9].
- Jan Kocbach. Finite element modeling of ultrasonic piezoelectric transducers.-University of Bergen Department of Physics.:September 2000
- J. H. Goll. The design of broad-band fluid-loaded ultrasonic transducers.- IEEE Trans. Sonics Ultrason. SU-26, 1979.
- J. W. Hunt, M. Arditi, and F. S. Foster. Ultrasound transducers for pulse-echo medical imaging, IEEE Trans. Biomed. Eng. BME-30, 1983.
- N. G. Pace and P. D. Thorne. Efficiency of face-plated underwater acoustic transducers. Ultrasonics 21, 1983.
- G. Kossoff. The effects of backing and matching on the performance of piezoelectric ceramic transducers. IEEE Trans. Sonics Ultrason. SU-13, 1966.
- N. Lamberti, G. Caliano, A. Iula, and M. Pappalardo. A new approach for the design of ultrasono-therapy transducers, IEEE Trans. Ultrason. Ferroelectr. Freq. Contr. 44, 1997.
- G. L. Wojcik, C. DeSilets, L. Nikodym, D. Vaughan, N. Abboud, and J. Mould Jr. Computer modeling of diced matching layers, in Proc. of 1996 IEEE Ultrason. Symp. IEEE, New York, 1996.
- I.Chilibon, M.Wevers, J.Lafaut. Ultrasound underwater transducer for extracorporeal shock wave lithotripsy.-Bucharest, Romania.: Romanian Reports in Physics, 2005
- Zensheu Chang, Stewart Sherrit, Xiaoqi Bao, and Yoseph Bar-Cohen., Design and analysis of ultrasonic horn for USDC (Ultrasonic/Sonic Driller/Corer).: NASA/JPL, USA, 2003
Библиографический список
engineering-solutions.ru
ультразвуковой пьезокерамический преобразователь — патент РФ 2448782
Изобретение относится к ультразвуковой технике, в частности к устройствам для интенсификации технологических процессов в жидких средах, и может найти применение в машиностроительной, электронной, фармацевтической промышленности, приборостроении и атомной энергетике. Ультразвуковой пьезокерамический преобразователь включает корпус с установленным в сквозном отверстии его излучающей мембраны, по крайней мере, одним излучателем, волновод которого соединен с корпусом с помощью сварного шва, дополнительно выполняющего функции демпфера гашения изгибных колебаний, при этом для работы в агрессивных средах корпус, излучатель и волновод выполнены из титана. А при установке в корпусе нескольких излучателей расстояние между ними выбирают предпочтительно равное одной четверти длины волны ультразвуковых колебаний. Предлагаемое изобретение упрощает конструкцию преобразователя, повышает эффективность ультразвуковых колебаний при работе в агрессивных средах и обеспечивает надежную герметизацию корпуса от протечек озвучиваемой жидкости. 4 з.п. ф-лы, 4 ил.
Рисунки к патенту РФ 2448782
Изобретение относится к ультразвуковой технике, а именно к устройствам для интенсификации технологических процессов в жидких средах: очистки деталей, экстракции, травления, пропитки, и может найти применение в машиностроительной, электротехнической, электронной, фармацевтической промышленности, приборостроении и атомной энергетике.
Известен целый ряд ультразвуковых пьезоэлектрических преобразователей, в которых элементы герметизации внутреннего их устройства от внешнего воздействия жидкой среды выполнены в виде фторопластовых или резиновых уплотнений. Всем им присущ общий недостаток: при установке их в мощных пьезопреобразователях они со временем разрушаются под действием ультразвука, в результате образуются протечки жидкости внутрь корпуса и излучатели выходят из строя. (См. Патент на полезную модель РФ № 66700, B06B 1/06 «Ультразвуковой пьезокерамический преобразователь», опубл. 10.11.2005 г., а также патент РФ на изобретение № 20090013, H04R 17/00 «Устройство крепления армированного пьезопреобразователя», опубл. 10.09.1997 г.)
Таким образом, все подобные преобразователи имеют ограниченное применение
Известен также погружной ультразвуковой преобразователь для озвучивания жидкости в ванне, который включает в свой состав корпуса пьезопластину, мембрану и элемент для закрепления преобразователя к ванне. Для осуществления герметизации внутренней полости преобразователя от протечки жидкости используется установленное в проточке корпуса уплотнительное кольцо. Для охвата большей площади озвучивания несколько преобразователей объединены в ванне в один ряд. Но и в этом преобразователе не решена проблема герметизации, поскольку возможно попадание жидкости во внутреннюю полость корпуса, вследствие износа уплотнительного кольца и ослабления резьбового соединения. (См. Патент РФ на изобретение № 2009720, B06B 1/06 «Ультразвуковой высокочастотный преобразователь для озвучивания жидкости в ванне», опубл. 30.03.1994 г.)
Также известен ультразвуковой пьезокерамический преобразователь для озвучивания жидкости, который содержит излучающую накладку, пьезопакет, армирующую шпильку, фланец, кольцевое уплотнение, гайку, шпильку для крепления к ванне, акустически развязывающую мембрану с уступом и демпфер. При этом фланец и уступ мембраны жестко связаны между собой сваркой. Дополнительная герметизация осуществляется резиновым или фторопластовым кольцом, которое притягивается к дну ванны перемещением гайки по шпильке.
Демпфирование от появления изгибных колебаний осуществляется пластмассовым кольцом. (См. Авторское свидетельство СССР № 1622025, B06B 1/06 «ультразвуковой пьезокерамический преобразователь для озвучивания жидкости», опубл. 23.01.1991 г.)
Основным недостатком данной конструкции является сложность узла крепления преобразователя ко дну ванны, к тому же используемое как уплотнение резиновое или фторопластовое кольцо не обеспечивает надежную долгосрочную герметизацию преобразователя от озвучиваемой им жидкости, особенно в случае агрессивного раствора кислот или щелочей.
Известен также и ультразвуковой пьезокерамический преобразователь с излучателем, установленный с внешней стороны дна емкости с элементом его крепления, выполненным в виде сварного шва и резьбового соединения. (См. Свидетельство на полезную модель РФ № 35250, МПК B06B 1/06, опубл. 10.01.2004 г.) Данный ультразвуковой пьезокерамический преобразователь использован в устройстве для очистки жидкости, включающем емкость, ко дну которой с внешней стороны прикреплен упомянутый преобразователь. При этом элемент крепления выполнен в виде втулки с внутренней резьбой, жестко закрепленной на дне емкости с помощью сварки, а излучатель снабжен внешней резьбой с возможностью ввинчивания его во втулку до упора в дно емкости. В этом устройстве, как следует из чертежа, проблема герметизации решена полностью за счет крепления излучателей к дну емкости с внешней стороны. Однако в этом случае не удается избежать потери интенсивности ультразвуковых колебаний, так как последние передаются, во-первых, через стенку емкости, а во-вторых, в резьбовом соединении обязательно образуется торцевой зазор, в котором также будет наблюдаться частичная потеря мощности излучения, потому что подогнать идеально поверхность дна емкости и торец излучателя практически невозможно.
Поэтому необходимо упростить конструкцию, исключив резьбовое соединение. Задача предлагаемого изобретения заключается в устранении недостатков аналогов и прототипа, а именно обеспечить полную герметизацию преобразователя от протечек озвучиваемой жидкости и добиться максимально возможной мощности излучения в рабочую жидкость.
Задача решается путем озвучивания непосредственно самой жидкости, находящейся в емкости для обработки изделий с одновременной нейтрализацией изгибных колебаний мембраны ультразвукового преобразователя.
Технический результат, заключающийся в упрощении конструкции преобразователя с одновременным повышением интенсивности ультразвуковых колебаний в жидкости, достигается за счет того, что, по крайней мере, один излучатель установлен в сквозном отверстии излучающей мембраны или мембранного дна корпуса с возможностью непосредственного контактирования его волновода с озвучиваемой жидкостью, при этом волновод, выполненный из материала с низким акустическим сопротивлением (титана) герметично соединен с корпусом преобразователя сварным швом, выполняющим дополнительную функцию демпфера для гашения изгибных колебаний излучающей мембраны. Для обеспечения качественного соединения сварным швом к корпусу излучателя его волновод выполнен Т-образной формы с головкой в виде буртика, который перекрывает отверстие мембранного дна по всему периметру на величину 2-5 мм, образуя зону однородного соединения из одного и того же металла Выполнение корпуса преобразователя и волновода излучателя из титана дает возможность использования его в агрессивных средах, а главное, титан обладает низким акустическим сопротивлением, что способствует минимизации потерь мощности ультразвуковых колебаний в волноводе излучателя, контактирующем с озвучиваемой жидкостью.
В описании устройства, взятого за прототип, отсутствуют какие-либо специальные требования к сварному шву и использование его в качестве демпфера, следовательно, этот шов предназначен только для крепления втулки ко дну емкости и в силу своего расположения и формы не может выполнять роль демпфера. В предлагаемом преобразователе сварной шов соединяет край буртика волновода с излучающей мембраной внахлест и его размер составляет 4-8 мм, т.е. идет дополнительное наплавление металла на излучающую поверхность корпуса преобразователя с иной структурой и плотностью материала. Сварной шов, выполненный в таком варианте, как показали испытания, служит хорошим демпфером, гасящим изгибные колебания лицевой мембраны корпуса преобразователя. В случае если в корпусе преобразователя установлено несколько излучателей, демпфер паразитных изгибных колебаний, выполненный в виде концентрично охватывающего волновод сварного шва, формирует вокруг каждого излучателя барьер, препятствующий возникновению изгибных волн как от собственного, так и о соседних излучателей, что и обеспечивает их развязку. Это, в конечном счете, также снижает потери мощности при передаче ультразвуковой энергии и повышает равномерность акустического поля в озвучиваемой жидкости. (См., например, патент РФ № 2188085, B08B 3/12, опубл. 27.08.2002 г.)
Благодаря развязке пьезоэлектрических излучателей за счет ослабления или препятствия передаче изгибных паразитных колебаний за пределы демпфирующего шва, появляется возможность увеличить плотность расположения излучателей на одном и том же поле излучения и, тем самым, повысить акустическую мощность преобразователя в целом.
Ультразвуковой пьезокерамический преобразователь является новым, поскольку в источниках информации совокупность предложенных признаков, отраженных в формуле изобретения, в том числе и в дополнительных пунктах, не обнаружена.
Предложенный ультразвуковой пьезокерамический преобразователь как техническое решение обладает изобретательским уровнем. Дело в том, что в промышленности, особенно в теплообменных системах, достаточно часто приходится удалять с поверхностей деталей и механизмов стойкие отложения солей и различные накипи, при этом используются растворы агрессивных сред в виде кислот и щелочей. Для удаления таких вредных отложений требуется мощное ультразвуковое излучение, в то же время ультразвуковой преобразователь должен иметь компактную форму и стойко выдерживать воздействие агрессивных сред. Предлагаемый ультразвуковой пьезокерамический преобразователь удовлетворяет этим требованиям. Высокая плотность расположения излучателей на мембране корпуса преобразователя, низкое акустическое сопротивление титана и непосредственное выведение рабочей поверхности волноводов излучателей в озвучиваемую жидкость позволяют обеспечить минимальную физически возможную по совокупности потерю интенсивности ультразвуковых колебаний и максимально возможную мощность кавитационного воздействия для удаления вредных отложений с обрабатываемых поверхностей.
Предложенное техническое решение не является очевидным, поскольку сварной шов, выполненный описанным выше образом, применяется не только в качестве элемента для крепления волновода излучателя к корпусу преобразователя, но и выполняет функцию демпфера гашения изгибных колебаний. Таким образом, две функции: крепления и гашения изгибных колебаний совмещены в одном признаке, что привело к упрощению ультразвукового преобразователи и, одновременно, к повышению интенсивности ультразвукового излучения.
Указанное конструктивное отличие и совмещение функций не было обнаружено в информационной, научно-технической литературе и патентных материалах, что свидетельствует о неочевидности и неординарности предлагаемого ультразвукового пьезокерамического преобразователя. Отмеченное отличие, по нашему мнению, нельзя отнести к методу обычного инженерного проектирования.
Изготовление и испытание опытных образцов показали их работоспособность и подтвердили получение технического результата, указанного в описании изобретения, что соответствует критерию «промышленная применимость».
Корпус преобразователя выполнен в герметичном исполнении и может быть применен в качестве погружного варианта, однако может быть установлен и в дне рабочей емкости.
Изобретение проиллюстрировано чертежами, где на фиг.1 изображен корпус ультразвукового пьезокерамического преобразователя с местным вырывом (вид сбоку), на фиг.2 показана излучающая мембрана с излучателями, расположенными в один ряд, на фиг.3 показана излучающая мембрана с излучателями, размещенными в два ряда, на фиг.4 отражен общий вид преобразователя для открытых емкостей с излучателем в разрезе. Ультразвуковой пьезокерамический преобразователь содержит корпус 1 с выполненным в дне или излучающей мембране 2 сквозным отверстием 3, в котором установлен, по крайней мере, один пьезокерамический излучатель 4, включающий звукопроводящий волновод 5 Т-образной формы с буртиком 6 и излучающей поверхностью 7, пакет пьезоэлементов 8, армирующую шпильку 9 и стальную гайку 10. Звукопроводящий волновод 5 излучателя 4, вставленный свободно в отверстие 3 дна или излучающей мембраны 2 (фиг.4), соединен посредством буртика 6 с излучающей мембраной или дном емкости сварным швом 11. Во всех случаях излучающая поверхность 7 волновода 5 контактирует с озвучиваемой жидкостью непосредственно, что увеличивает интенсивность ультразвуковых колебаний. Сварной шов выполняется аргонно-дуговой сваркой в среде инертных газов. Для обеспечения качественного сварного соединения излучателя 4 с излучающей мембраной 2 или дном емкости и надежной работы шва в качестве демпфера изгибных колебаний, диаметр буртиков должен быть больше диаметра излучателя d2 на 4-10 мм, т.е. буртик 6 должен перекрывать отверстие 3 по всему его периметру не менее чем на 2 мм, а внешний диаметр шва d3 должен быть больше диаметра буртика 6 на 10-12 мм или быть по ширине равным 5-6 мм. Толщина буртика 6 находится в пределах 0,8-1,0 мм и равна толщине стенки корпуса 1. Все размеры подобраны экспериментально и обусловлены возможностью максимальной передачи ультразвуковых колебаний в озвучиваемую жидкость, чтобы обеспечить эффективное удаление отложений или накипей с обрабатываемых поверхностей.
Для обеспечения максимальной проводимости ультразвука и возможности работы преобразователя в агрессивных следах его корпус, излучатель и волновод выполняются из титана, допустимо их изготовление из нержавеющей стали, однако интенсивность ультразвуковой кавитации за счет более высокого акустического сопротивления нержавеющей стали будет при этом ниже. Далее, ввиду того, что титановый волновод имеет меньшее акустическое сопротивление, чем стальная гайка 10, работающая как отражатель, амплитуда колебаний на излучающей поверхности 7 будет выше, т.е. излучатель 4 работает в режиме одностороннего излучения, увеличивая поток акустической энергии в озвучиваемую жидкость.
При больших размерах емкости или излучающей мембраны 2 преобразователя на их поверхности могут быть установлены несколько излучателей 4 в один (фиг.2) или несколько рядов (фиг.3). Для подвода электроэнергии к пьезоэлементам пакета 8 предусмотрен штуцер 12. А для закрепления корпуса 1 преобразователя по месту обработки установлены уголки 13.
Ультразвуковой керамический пьезопреобразователь работает следующим образом.
При подаче генератором (на фиг. не показан) электрических колебаний ультразвуковой частоты (20-25 кГц) через штуцер 13 на пакет пьезоэлементов 8, в них под действием пьезоэлектрического эффекта происходит преобразование электрической энергии в энергию механических колебаний, которые через звукопроводящий титановый волновод 5, излучающую поверхность 7 поступают непосредственно в озвучиваемую жидкость, вызывая ее кавитацию. Под действием кавитации происходит активное перемешивание озвучиваемой жидкости и микровзрывы в ней, за счет чего и происходит преодоление сил адгезии удаляемых отложений и накипей.
Сварной шов 11 при этом обеспечивает герметичность корпуса 1, защищая его от протечек озвучиваемой жидкости, в то же время шов служит демпфером для гашения паразитных изгибных колебаний в излучающей мембране, или дне 2 корпуса преобразователя. При соединении при помощи сварного концентрической формы шва 11 волновода 5 излучателя с корпусом 1 образуется 3 зоны, переходящие одна в другую. При этом зоны имеют различную толщину, плотность, структуру. Так, толщина буртика 6 и стенки корпуса 1, которая переходит в сварной шов 11 с уклоном к его периферии, и толщина стенки самого корпуса 1 представляют как раз неоднородную систему, в которой изгибная волна, отражаясь и складываясь, заметно гасится, что повышает эффективность развязки преобразователей и повышает равномерность ультразвукового поля. При этом, если толщина буртика 6 волновода 5 и стенки корпуса 1 будет менее 0,8-1,0 мм, то усложняются условия сварки, а при толщине более 1,0 мм снижается интенсивность ультразвуковых колебаний лицевой излучающей мембраны или дна 2 корпуса 1. Установленные экспериментально величины ширины сварного шва 11 в 5-6 мм и перекрытия буртиком 6 отверстия 3 на 2-5 мм обусловлены условиями сборки преобразователя, качеством сварного шва и эффективностью ультразвукового излучения.
Излучатели 4 для создания плотного и равномерного ультразвукового поля должны располагаться достаточно плотно, предпочтительно расстояние между ними выбирается равным одной четверти длины волны, т.е. /4.
Все вышеперечисленные конструктивные отличия предлагаемого преобразователя, а также развиваемая им интенсивность ультразвуковых колебаний, составляющих 2,4-2,7 Вт/см2 при максимальном КПД, позволяет преодолеть силы адгезии таких вредных технологически образуемых покрытий, как отложения солей или накипи.
Предложенный преобразователь реализован в ультразвуковых ваннах и в конструкции погружного ультразвукового пьезокерамического преобразователя, которые изготовлены, испытаны с получением технического результата, указанного в описании изобретения, т.е. подтверждено, что они работоспособны, просты в изготовлении, обеспечивают надежную герметичность корпуса от протечек озвучиваемой жидкости и высокую интенсивность ультразвуковых колебаний.
Источники информации
1. Патент РФ на полезную модель № 84971, МКИ B06B 1/06, G01F 1/66, опубл. 21.01.2009 г.
2. Авторское свидетельство СССР № 631219, МКИ B088B 3/12, опубл. 05.11.1978 г.
3. Патент США № 4957669, B068B 3/00, опубл. 18.09.1990 г.
4. Заявка E11B 0420190, B068B 1/06, H04R 17/00, опубл. 03.04.1991 г.
5. Заявка ФРГ № 4014199, B06B 1/06, H04R 17/100, опубл. 22.11.1990 г.
ФОРМУЛА ИЗОБРЕТЕНИЯ
1. Ультразвуковой пьезокерамический преобразователь, включающий корпус с установленным в нем с использованием сварки излучателем с волноводом ультразвуковых колебаний, отличающийся тем, что, по крайней мере, один излучатель установлен в сквозном отверстии лицевой излучающей мембраны или дна корпуса с возможностью непосредственного контакта излучающей поверхности волновода с озвучиваемой жидкостью, при этом волновод из акустически прозрачного материала герметично соединен с корпусом преобразователя сварным швом, выполняющим дополнительную функцию демпфера гашения изгибных колебаний.
2. Ультразвуковой пьезокерамический преобразователь по п.1, отличающийся тем, что его корпус и волновод излучателя выполнены из титана или нержавеющей стали.
3. Ультразвуковой пьезокерамический преобразователь по п.1, отличающийся тем, что волновод излучателя ультразвуковых колебаний выполнен Т-образной формы с головкой в виде буртика для присоединения его к корпусу преобразователя, при этом буртик перекрывает отверстие по всему периметру на 2-5 мм.
4. Ультразвуковой пьезокерамический преобразователь по п.1, отличающийся тем, что ширина сварного шва, соединяющего буртик волновода с корпусом преобразователя, составляет 5-6 мм.
5. Ультразвуковой пьезокерамический преобразователь по п.1, отличающийся тем, что при установке в корпусе нескольких излучателей расстояние между ними предпочтительно составляет около одной четверти длины волны ультразвуковых колебаний.
www.freepatent.ru
Ультразвуковой шокер излучатель — Старые схемы шокеров — Статьи к прочтению — Электрошокер
Ультразвуковой шокер-излучатель
Исполнительное устройство активной сигнализации
Данное устройство предназначено только для демонстрационных испытаний в лабораторных условиях. Предприятие не несет ответственности за любое использование данного устройства.
Ограниченный сдерживающий эффект достигается воздействием мощного ультразвукового излучения. При сильных интенсивностях, ультразвуковые колебания производят чрезвычайно неприятный, раздражающий и болезненный эффект на большинство людей, вызывая сильные головные боли, дезориентацию, внутричерепные боли, паранойю, тошноту, расстройство желудка, ощущение полного дискомфорта.
Генератор ультразвуковой частоты выполнен на D2. Мультивибратор D1 формирует сигнал треугольной формы, управляющий качанием частоты D2. Частота модуляции 6-9 Гц лежит в области резонансов внутренних органов.
D1, D2 — КР1006ВИ1; VD1, VD2 — КД209; VT1 — KT3107; VT2 — KT827; VT3 — KT805; R12 — 10 Ом;
T1 выполнен на ферритовом кольце М1500НМЗ 28х16х9, обмотки n1, n2 содержат по 50 витков D 0.5.
Отключить излучатель; отсоединить резистор R10 от конденсатора C1; подстроечным резистором R9 выставить на выв. 3 D2 частоту 17-20 кГц. Резистором R8 установить требуемую частоту модуляции (выв. 3 D1). Частоту модуляции можно уменьшить до 1 Гц, увеличив емкость конденсатора С4 до 10 мкФ; Подсоединить R10 к С1; Подключить излучатель. Транзистор VT2 (VT3) устанавливают на мощный радиатор.
В качестве излучателя лучше всего применить специализированную пьезокерамическую головку ВА импортного или отечественного производства, обеспечивающую при номинальном напряжении питания 12 В уровень звуковой интенсивности 110 дБ: Можно использовать несколько мощных высокочастотных динамических головок (динамиков) ВА1…BAN, соединенных параллельно. Для выбора головки, исходя из требуемой интенсивности ультразвука и расстояния действия, предлагается следующая методика.
Средняя подводимая к динамику электрическая мощность Рср = Е2 / 2R, Вт, не должна превышать максимальной (паспортной) мощности головки Рmaх, Вт; Е — амплитуда сигнала на головке (меандр), В; R — электрическое сопротивление головки, Ом. При этом эффективно подводимая электрическая мощность на излучение первой гармоники Р1 = 0.4 Рср, Вт; звуковое давление Рзв1 = SдP11/2/d, Па; d — расстояние от центра головки, м; Sд = S0 • 10(LSд/20) Па Вт-1/2; LSд — уровень характеристической чувствительности головки (паспортное значение), дБ; S0 = 2 • 10-5 Па Вт-1/2. В результате, интенсивность звука I = Npзв12 / 2sv, Вт/м2; N — число параллельно соединенных головок, s = 1.293 кг/м3 — плотность воздуха; v = 331 м/с — скорость звука в воздухе. Уровень интенсивности звука L1 = 10 lg (I/I0), дБ, I0 = 10-12 I m/м2.
Уровень болевого порога считается равным 120 дБ, разрыв барабанной перепонки наступает при уровне интенсивности 150 дБ, разрушение уха при 160 дБ {180 дБ прожигает бумагу). Аналогичные зарубежные изделия излучают ультразвук с уровнем 105-130 дБ на расстоянии 1 м.
При использовании динамических головок дли получения требуемого уровня интенсивности может потребоваться увеличить напряжение питания. При соответствующем радиаторе (игольчатый с габаритной площадью 2 дм2) транзистор KT827 (металлический корпус) допускает параллельное включение восьми динамических головок с сопротивлением катушки 8 0м каждая. 3ГДВ-1; 6ГДВ-4; 10ГИ-1-8.
Разные люди переносят ультразвук по разному. Наиболее чувствительны к ультразвуку люди молодого возраста. Дело вкуса, если вместо ультразвука вы предпочтете мощное звуковое излучение. Для этого необходимо увеличить емкость С2 в десять раз. При желании можно отключить модуляцию частоты, отсоединив R10 от С1.
С ростом частоты эффективность излучения некоторых типов современных пьезоизлучателей резко увеличивается. При непрерывной работе более 10 минут, возможен перегрев и разрушение пьезокристалла. Поэтому рекомендуется выбирать напряжение питания ниже номинального. Необходимый уровень звуковой интенсивности достигается включением нескольких излучателей.
Ультразвуковые излучатели обладают узкой диаграммой направленности. При использовании исполнительного устройства для охраны помещений большого объема излучатель нацеливают в направление предполагаемого вторжения.
Взято с http://patlah.ru/etm/etm-11/e-shokeri/e-shokeri/e-shok-09.html
© «Энциклопедия Технологий и Методик» Патлах В.В. 1993-2007 гг.
elektroshoker.org
Ультразвук
Ультразвук в промышленностиСпособность ультразвука распространяться внутри любого материала в виде луча, а также активное взаимодействие ультразвука с веществом на уровне атомов и молекул легли в основу создания ряда технологических установок, применяемых как в легкой, так и в тяжелой промышленности.
Такими были станки ультразвуковой обработки материала в 1950-1970 годах.
Современные ультразвуковые станки
Кроме механической обработки материалов в любом производстве требуется контроль качества выпускаемой продукции, и ультразвуковая диагностика изделия позволяет неразрушающим методом воздействия повысить рентабельность производства. Современные диагностические ультразвуковые приборы могут быть компактными и многофункциональными.
Современный ультразвуковой дефектоскоп
В зависимости от конкретных задач частота ультразвука может быть низкой (ультразвуковая резка, сварка, пайка, очистка ) или же высокой ( ультразвуковая дефектоскопия, измерение толщины слоя материала, измерение остаточного напряжения ). При этом мощность ультразвукового генератора также зависит от конкретного применения ( от нескольких милливатт до киловатта ).
Блок ультразвуковой колебательной системы любого технологического станка состоит из четырех конструктивных элементов: преобразователя, волновода, концентратора акустической энергии и излучателя. Хотя в некоторых моделях станков волновод отсутствует, и преобразователь закрепляется на концентраторе.
1- Ультразвуковой преобразователь (магнитострикционный)
2- Акустический волновод
3- Акустический концентратор
4- Излучатель
Схема колебательной системы и распределение смещения по длине колебательной системы
Преобразователь осуществляет преобразование электрической энергии в энергию акустических колебаний. В качестве преобразователя применяют или магнитострикционный, или пьезокерамический вибратор.
Концентратор акустической энергии служит трансформатором упругих колебаний, с помощью которого можно в несколько раз увеличить амплитуду ультразвуковых колебаний вибратора.
Концентраторы изготавливаются из монолитного металлического стержня, как правило, имеющего разное поперечное сечение. Возможные варианты концентраторов приведены на рисунке.
1- Стержень постоянного сечения
2- Ступенчатый стержень
3- Экспоненциальный стержень
Излучатель представляет собой рабочий инструмент, выполненный в виде съемной насадки к акустическому концентратору. Излучатель может иметь самые разнообразные формы в зависимости от конкретного назначения ультразвукового станка.
Ультразвуковая сварка
Ультразвуковая сварка-это образование прочной связи между твердыми материалами под действием ультразвука. С помощью ультразвуковой сварки осуществляется прочное соединение металлических или пластмассовых листов, а также проволок. Максимальная толщина свариваемых изделий зависит от конкретного материала. При ультразвуковой сварке металлических листов или проволок толщина исходных заготовок находится в пределах 10 мкм- 2,5 мм ( чем больше твердость и тугоплавкость металла, тем меньше возможная толщина сварки ).
Не вдаваясь в подробности, суть ультразвуковой сварки можно объяснить тем, что под действием ультразвука свариваемые изделия подвергаются воздействию статической силы сдавливания и силы поперечных колебаний. Когда механическое напряжение в обрабатываемых материалах превысит их предел упругости, поверхностные слои материалов разрушаются и смешиваются между собой, образуя сварное соединение. Если поверхность свариваемых изделий гладкая и ровная, прочность сварного соединения практически равна прочности основного материала.
Возможные схемы ультразвуковых сварочных станков показаны на рис.1, рис.2, рис.3.
1- Стойка
2- Кронштейн сварочной головки
3- Пружина возврата
4- Рабочий стол
5- Рычаг
1, 10- Сварочные головки
2- Стойка
3- Стол
4- Противовес
5- Тяга
6- Рычаг с ножной педалью
7- Регулировочный винт
8- Пружина
9- Стакан
1- Хобот
2- Стол
3- Двигатель
4- Кулачок
5- Пружина
6- Опора
Свариваемые изделия сжимаются между монолитным основанием и прижимающим стержнем-звукопроводом, через который подается ультразвук. Для эффективного воздействия ультразвука под монолитное основание подкладывается эластичная прокладка ( силикон, резина ). При использовании прокладки большая часть ультразвуковой энергии будет оставаться в зоне сварки, и лишь незначительная часть ультразвука уйдет в землю.
Также применяется пружинный прижим рабочего стола к обрабатываемому материалу. Один из вариантов показан на рисунке ниже.
1- Волновод
2- Стол сварочного станка
3- Стакан
4- Подвижная втулка
5- Пружина
6- Регулировочный винт
7- Концевой выключатель
8- Рабочий стол
В процессе сварки ультразвук действует не только на свариваемые изделия, но и на стержень-звукопровод. Для предотвращения образования сварного соединения между обрабатываемой деталью и стержнем-звукопроводом применяют наконечник из тугоплавкого и износостойкого материала. Наконечник, закрепляемый на выходном торце стержня-звукопровода, делается съемным, что позволяет получить несколько вариантов сварного соединения.
В маломощных установках ( мощность ультразвукового генератора 1-100 Вт ) используемых для точечной сварки наконечник имеет сферическую или плоскую форму. Для сваривания длинных листов в мощных установках ( мощность ультразвукового генератора 1-30 кВт ) наконечник имеет форму прямоугольного сечения.
Для справки:
Частота ультразвука технологических станков находится в пределах 10-100 кГц.
Низкие частоты ( 10-20 кГц ) имеют мощные установки с питанием от машинных генераторов ( до 30 кВт ). Такие установки осуществляют шовное сварное соединение. Скорость сварки достигает 10 м/мин.
Повышенные частоты ( 50-100 кГц ) имеют установки малой и средней мощности с питанием от лампового или полупроводникового генератора ( до 100 Вт ). Такие установки осуществляют точечную сварку.
В установках ультразвуковой сварки применяют как магнитострикционные, так и пьезокерамические излучатели.
При прочих равных условиях твердые и толстые материалы требуют большей мощности ультразвукового генератора для образования сварного соединения, чем мягкие и тонкие материалы. Легче всего свариваются тонкие изделия, т.к. требуемая энергия ультразвука может быть незначительной. Для сварки тонких полимерных пленок, а также точечной сварки вполне достаточно усилия руки, чтобы прижать концентратор к зоне сварки.
Ручная сварка тонких листов ультразвуковым пистолетом
Фотография современного ультразвукового пистолета для точечной сварки
Ультразвуковую сварку применяют, прежде всего, в тех случаях, когда требуется прочное соединение материалов, которых нельзя подвергать воздействию высокой температуры. Кроме того, ультразвуковая сварка позволяет прочно соединять разнородные материалы ( например, алюминий с нержавеющей сталью ).
Ультразвуковая сварка находит широкое применение и в микроэлектронике при изготовлении миниатюрных изделий ( контактные провода и площадки диодов, транзисторов или микросхем ).
Ультразвуковую сварку используют также и при производстве различных упаковочных пакетов и контейнеров.
Ультразвуковая резка
Ультразвуковая резка-это своеобразный отбойный молоток, действующий на микроскопическом уровне. В роли молота выступает ультразвуковой излучатель. Даже ультразвуковая кавитация способна вырезать причудливые узоры. Однако кавитационное разрушение материала происходит, главным образом, на поверхности ультразвукового излучателя, а в основе работы аппарата ультразвуковой резки лежит принцип ударного воздействия абразивного зерна на поверхность твердого тела.
Кавитационная эрозия торца ферритового стержня
Если работающий ультразвуковой вибратор прижать к какой-либо твердотельной поверхности, находящейся в жидкости, начнется активное воздействие ультразвука на поверхность твердого тела. Добавление абразивного порошка ускорит этот процесс ( к кавитации добавляется удар зерном абразива ). В результате на поверхности твердого тела образуется углубление, профиль которого точно повторяет форму торца вибратора, т.е. материал разрушается в плоскости, перпендикулярной к направлению ультразвуковых колебаний.
1- Обрабатываемая деталь
2- Инструмент
3- Суспензия абразива
F пр — Статическая сила прижима
Схема работы аппарата ультразвуковой резки поясняется на рисунке ниже.
1- Преобразователь
2- Ультразвуковой генератор
3- Волновод-концентратор
4- Инструмент
5- Система крепления (концентратор закрепляется в узловых точках колебаний )
6- Обрабатываемая деталь
7- Подача суспензии абразива
8- Пружина
Обрабатываемая деталь помещается на монолитное основание, и на деталь непрерывно подается суспензия абразива. Над обрабатываемой деталью находится ультразвуковой вибратор, крепление которого позволяет совершать движение вверх-вниз подобно сверлильному станку. Как правило, все установки ультразвуковой резки используют акустический концентратор, позволяющий увеличить амплитуду ультразвуковых колебаний в зоне обработки. К тому же, наличие концентратора позволяет использовать несколько сменных разнопрофильных головок. Головка-резец крепится на выходном конце концентратора и в процессе работы с некоторым усилием прижимается к обрабатываемой детали. Возникающие при ультразвуковой резке мельчайшие частицы обрабатываемой детали, а также изношенный абразив удаляются из зоны резки непрерывной подачей жидкости со свежими зернами абразива.
Применяемая на практике колебательная система станка ультразвуковой резки показана на рисунке ниже.
1- Преобразователь
2- Концентратор
3- Инструмент
4- Резонансный фланец
5- Корпус станка
Скорость ультразвуковой резки зависит от многих параметров и не является постоянной величиной. С увеличением глубины резки скорость снижается и может упасть до нуля при глубине более 15 мм. Причина тому, уменьшение концентрации абразивных зерен под головкой-резцом с ростом глубины обработки.
Кроме того, производительность установки ультразвуковой резки зависит от частоты и мощности ультразвука (при увеличении частоты и амплитуды ультразвуковых колебаний скорость резки возрастает ).
Для справки:
Частота ультразвука в технологических станках находится в пределах 18-22 кГц, а мощность ультразвукового генератора 0,4-4 кВт. В качестве ультразвукового вибратора применяют магнитострикционный вибратор, набранный из металлических пластин.
Важное значение имеет и абразив ( карбид бора, карбид кремния ). Для эффективной ультразвуковой резки твердость абразивного зерна должна быть выше твердости обрабатываемого материала. Чем мельче абразивное зерно, тем точнее резка. Однако при этом уменьшается скорость резки, и при очень мелком зерне процесс резки прекращается.
При прочих равных условиях хрупкие материалы обрабатываются быстрее, чем вязкие ( скорость обработки стекла в 16 раз выше скорости обработки латуни ).
Ультразвуковую резку применяют при обработке, главным образом, хрупких и твердых материалов, таких как стекло, пластины кремния или германия, керамика, ювелирные самоцветы.
Ультразвуковая очистка
В основе работы ультразвуковых установок очистки лежит явление ультразвуковой кавитации. При захлопывании кавитационного пузыря образуется микроскопическая кумулятивная струя, способная разрушить любой материал, находящийся под ее воздействием. Даже образование на поверхности очищаемого объекта кавитационного пузыря приводит к отслаиванию пленки загрязнения.
1- Начальная фаза отслоения
2- Откалывание кусочка пленки
Процесс кавитации происходит в жидкости, поэтому для ультразвуковой очистки требуется резервуар с жидкостью, в которую погружается очищаемый обьект. Ультразвуковые колебания в жидкости создаются или непосредственным вводом ультразвукового излучателя в жидкость, или через звукопровод ( ультразвуковой вибратор находится за пределами резервуара с жидкостью ). Существует также и контактный метод, когда очищаемый объект помещается в жидкость, а ультразвуковой вибратор имеет непосредственный контакт с очищаемым объектом. Контактный метод применяют для очистки крупногабаритных изделий со сложным профилем.
В промышленных установках ультразвуковой очистки резервуар изготавливается из нержавеющей стали, а ультразвуковой вибратор подключается к внешней стороне ( снизу, сбоку или комбинированный вариант ) резервуара.
Промышленная установка линии ультразвуковой очистки
Портативная ванна ультразвуковой очистки мелкогабаритных деталей
Для справки:
Частота ультразвука в технологических установках ультразвуковой очистки находится в пределах 18-44 кГц, а мощность ультразвукового генератора составляет 20-4000 Вт.
На низких частотах ультразвука применяют магнитострикционные вибраторы, а на повышенных частотах-пьезокерамические вибраторы.
Выбор жидкости зависит от конкретных объектов, подвергаемых очистке, а также от характера загрязнений. Обычно используют воду с добавками ПАВ ( поверхностно активное вещество ) или растворитель ( трихлорэтан, трихлортрифторэтан, метиленхлорид ). Воду применяют для удаления нерастворимых загрязнений типа микрочастиц твердого вещества. Растворитель применяют для удаления с поверхности очищаемого объекта загрязнения органического происхождения типа тяжелых масел, смазочных веществ, смола, битумные материалы и т.д. При этом очищению способствует химическое взаимодействие растворителя с веществом-загрязнителем.
Ультразвуковая очистка эффективна, прежде всего, при очистке мелких деталей и изделий, а также труднодоступных элементов конструкции. Основными отраслями промышленности, где используется ультразвуковая очистка являются электронная ( очистка электронных плат и электронных компонентов ) и автомобильная ( поршни и клапаны, карбюраторы, топливные форсунки и т.д. ) промышленности. Кроме того, ультразвуковую очистку применяют в медицине, авиации, приборостроении, часовом производстве и производстве ювелирных изделий, оптике и прикладных инженерных задачах.
Главное преимущество ультразвуковой очистки перед другими методами удаления загрязнений-это быстрота и качество очистки.
Ультразвуковая дефектоскопия
Распространение и отражение ультразвуковых волн подобно лучу света. Если в оптике, просвечивая световым лучом вещество, можно определить его оптическую однородность, то в ультразвуковой акустике по распространению в веществе упругих волн можно узнать о механической однородности вещества. Пропуская ультразвук через твердое тело, можно выявить наличие внутри твердого тела различные дефекты ( например, пустоты и трещины ). Как известно, на границе твердое тело-газ коэффициент отражения ультразвука очень высок. Таким образом, наличие в веществе микропустот приведет к ослаблению проходящей через вещество ультразвуковой волны, и по степени ослабления можно определить внутреннюю однородность вещества. На этом принципе работают различные ультразвуковые дефектоскопы ( сонометр ).
На рисунках ниже: 1- передатчик ультразвука, 2- приемник ультразвука, 3- проверяемый объект
Образец без дефектов
Образец с незначительным дефектом
Образец с большим дефектом
Ультразвуковой вибратор и приемник ультразвука прижимаются к исследуемому объекту противоположно друг другу. Акустический контакт между вибратором и объектом, а также объектом и приемником обеспечивается каплей жидкости ( например, машинное масло ). Чем выше частота ультразвука, тем меньший по размерам дефект можно выявить. Причина этому-дифракция. Если размеры дефекта близки к длине волны ультразвука, происходит огибание волной препятствия, и наличие внутренних дефектов не приведет к ослаблению проходящего через вещество ультразвука. Однако с ростом частоты ультразвука растет и его поглощение в веществе, что уменьшает возможную толщину исследуемого объекта. С другой стороны, если размер дефекта намного больше длины волны ультразвука, ультразвуковой луч может затеняться дефектом и не достигнуть приемника. Поэтому в ультразвуковой дефектоскопии методом просвечивания выбор частоты ультразвукового генератора определяется размерами выявляемых дефектов. Так при использовании ультразвука частотой 10 МГц можно обнаружить дефекты размером 0,5 мм в листовом железе толщиной 5 мм, а при дефектоскопии автомобильных покрышек на частоте ультразвука 100 кГц обнаруживаются дефекты размером порядка 10 мм. Дефекты железобетонных балок выявляются на частоте порядка 30 кГц.
Обнаружить внутренние дефекты в твердом теле можно не только, пропуская через него ультразвук, но и использовать отражение ультразвука от дефектов структуры вещества. На этом принципе работают ультразвуковые рефлектоскопы. Однако частотный диапазон ультразвукового генератора смещен в большую сторону, и частота измеряется мегагерцами.
Также как и сонометре ультразвуковой вибратор и приемник прижимаются к исследуемому объекту через каплю жидкости ( акустический контакт ). Однако в рефлектометре вибратор и приемник размещаются рядом, что делает весь прибор портативным. Большинство рефлектометров работает в импульсном режиме, что позволяет совместить вибратор и приемник в одном преобразователе, который поочередно работает как вибратор и как приемник ( прямой и обратный пьезоэффект ).
В режиме вибратора ультразвуковой преобразователь ( зонд ) посылает в объект ультразвуковую волну, которая отражаясь от задней поверхности объекта возвращается обратно к зонду. Если зонд перевести в режим приемника, он зафиксирует отраженную волну. При наличии в объекте дефекта отраженная от него ультразвуковая волна дойдет до зонда раньше, чем волна, отраженная от задней поверхности объекта, что регистрируется цифровым или аналоговым устройством. Таким образом, сканируя зондом объект, можно выявить не только наличие в нем дефектов, но и определить их глубину залегания.
Ультразвуковая дегазация
Как известно, любая жидкость, контактирующая с атмосферным воздухом, содержит в себе определенное количество растворенных в ней газов. Даже в расплавленном металле присутствует воздух. В металлургии и стекольной промышленности при отливке изделий крайне нежелательно наличие газа в расплаве, т.к. это приводит к возникновению микропор, что заметно снижает качество продукции.
Одним из методов удаления газа из жидкости является ультразвуковая дегазация, т.е. удаление газа посредством ультразвука. Под действием ультразвука в жидкости образуются области разряжения, в которые проникают молекулы газа, образуя газовые микропузыри. Микропузыри всплывают на поверхность жидкости ( расплава ), и тем самым происходит дегазация жидкости ( расплава ).
Введение ультразвука в расплав может реализовываться как в плавильном тигле, так и на этапе разлива расплава по формам. Ультразвук от вибратора, в качестве которого используется или магнитострикционный излучатель, или пьезоизлучатель, подводится в расплав через акустический волновод. Материал волновода выбирается таким, чтобы взаимодействие между расплавом и волноводом было как можно меньшим ( обычно используют фарфоровые волноводы ).
Ультразвуковая пайка
Облучение ультразвуком разнородных металлов позволяет создавать поверхностное интерметаллическое соединение, что используется при соединении металлических конструкций методом пайки. Припоем служит сплав на основе олова. В ходе пайки твердый припой расплавляется до образования жидкости, в которую вводят ультразвук. Если теперь в расплавленный припой поместить какой-либо металл, он вскоре покроется пленкой припоя.
Процесс лужения проходит достаточно быстро, и в промышленности применяют даже ручные ультразвуковые пистолеты, которыми работают как обычным паяльником. Таким ультразвуковым паяльником можно спаять практически любые металлы и даже керамику, но паяют, главным образом, сплавы на основе алюминия, т.к. обычная термическая пайка алюминия затруднена образованием тонкого слоя окиси алюминия на поверхности спаиваемых деталей. Ультразвуковой паяльник может иметь различную конструкцию, но обычно жало паяльника служит одновременно акустическим концентратором, на который намотана нагревательная обмотка, т.е. жало паяльника служит как для разогрева спаиваемых деталей, так и для ввода ультразвука в расплавленный припой. Частота ультразвукового генератора выбирается в пределах 20-30 кГц. Хотя в некоторых моделях используется пъезокерамический преобразователь, работающий на частоте 60 кГц.
На рисунке ниже представлен схематичный разрез одного из вариантов ультразвукового паяльника.
Современный ручной ультразвуковой паяльник
ultrasound.ucoz.ru
МОДЕРНИЗИРОВАННАЯ УЛЬТРАЗВУКОВАЯ ПУШКА «ИГЛА-М»
МОДЕРНИЗИРОВАННАЯ УЛЬТРАЗВУКОВАЯ ПУШКА «ИГЛА-М»
Ультразвук — это упругие волны высокой частоты. Обычно ультразвуковым диапазоном считают полосу частот от 20 000 до нескольких миллиардов герц. Сейчас ультразвук широко применяется в различных физических и технологических методах. То, что ультразвук активно воздействует на биологические объекты (например, убивает бактерии), известно уже более 70 лет. Электронная аппаратура со сканирующим ультразвуковым лучом используется в нейрохирургии для инактивации отдельных участков головного мозга мощным сфокусированным высокочастотным пучком. Высокочастотные колебания вызывают внутренний разогрев тканей.
До сих пор идут дискуссии о физическом влиянии ультразвуковых колебаний на клетку и даже о возможном нарушении структур ДНК. Более того, существуют сведения о том, что на микроуровне — не на уровне строения тела, а на каком-то более тонком, ультразвуковое воздействие оказывается вредным.
Ультразвук можно получить от механических, электромагнитных и тепловых источников. Механическими излучателями обычно служат разного рода сирены прерывистого действия. В воздух они испускают колебания мощностью до нескольких киловатт на частотах до 40 кГц. Ультразвуковые волны в жидкостях и твердых телах обычно возбуждают электроакустическими, магнитострикционными и пьезоэлектрическими преобразователями.
В промышленности давно уже изготавливают девайсы для ультразвукового воздействия на животных, например такие:
Назначение
Миниатюрный отпугиватель собак представляет собой носимый электронный прибор (собран в корпусе минифонарика), излучающий ультразвуковые колебания, слышимые собаками и не воспринимаемые человеком.
Принцип действия
Прибор разработан для защиты от нападения собак: ультразвуковое излучение определенной мощности обычно останавливает агрессивно настроенную собаку на расстоянии 3 — 5 метров или обращает ее в бегство. Наибольший эффект достигается при воздействии на агрессивных бродячих собак.
Технические характеристики
- Напряжение питания (1 аккумулятор типа 6F22 (KRONA)), В 9
- Ток потребления, не более, А 0,15
- Масса с аккумуляторами, не более, г 90
Как Вы понимаете, это слабая игрушка, но мы сделаем девайс гораздо мощнее! Продолжая эксперименты с ультразвуком (смотрите статью на сайте — ультразвуковая пушка»игла»), было сделано ряд интересных усовершенствований и доработок. Так был произведён революционный метод воздействия (естественно негативного), на живой организм двух ультразвуковых излучателей с разностной частотой несколько герц. То есть частота одного излучателя например 20000 Гц, а другого — 20010 Гц. В результате на ультразвуковое излучение накладывается инфразвуковое, что многократно усиливает деструктивный эффект!
Схема стандартная, генератор на CD4069 + усилитель на трёх Н-П-Н транзисторах. Питание не менее 12 В, при токе до 1 А.
Для усиления направленного эффекта используем цилиндрические звуковые резонаторы. Их роль будет выполнять обычная никелированная трубка от пылесоса. Только не надо портить пылесос, трубка отдельно продаётся на базаре или в магазине запчастей.
Обрезаем два куска на экспериментально определённую длинну (где-то пару сантиметров), и прикрепляем их к ВЧ головкам типа 5ГДВ-4 или любых других. Можно купить двойную насадку на выхлопную трубу автомобиля, монтаж гораздо удобнее, а эффект будет ещё лучше.
Внутрь вставляем ВЧ динамики, в задней части монтируем плату с аккумулятором.
Схемы для начинающихelwo.ru